Press Releases and News
Dr. Hönle AG will present its wide range of modern UV curing devices at the Battery Show Europe in Stuttgart from June 3 to 5, 2025.
Featured for discussion will be the curing of UV adhesives used in the production of cell contact systems. In this process, individual battery cells are combined into modules, interconnected via cell connectors, and finally combined into an overall storage system. Hönle is presenting the LED Powerline 820 AC IC system, which offers high-intensity irradiation and enables precise curing in seconds. The LED Powerline systems are modularly adaptable, and can be matched to the specific curing requirements of each selected adhesive.
An additional featured application involves the curing (or drying) of insulating UV coatings for battery cell housings. Similar to paint, these mostly blue colored coatings are sprayed onto the housings to provide insulation and corrosion protection between the cells. The LED SPOT 100 IC system from Hönle optimizes curing times to provide faster throughput and improved efficiency. This high-intensity LED flood system delivers reliable performance with the highest standard of quality.
"With our innovative UV technologies, both from the Adhesive Systems business unit and the Curing business unit, we offer customized solutions for battery production. We look forward to presenting our latest developments at the Battery Show Europe in Hall 7, Stand B 61 and discussing the future of battery technology with our partners," says Florian Diermeier, Director Sales UV Equipment at Dr. Hönle AG, Business Units Adhesive Systems.
More info about our uv curing systems
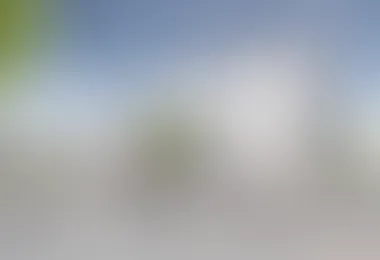
The welding points of a cell contacting system are covered with blue adhesive to protect against vibrations and corrosion
Dr. Hönle AG has developed a new lens type for its bluepoint LED UV curing unit series, which focuses the light into a linear irradiation and can therefore cure adhesives with a significantly higher intensity. The high intensity is usually required for applications in which a gap must be irradiated, such as active alignment.
The new optic can simply be screwed onto the LED heads of the bluepoint LED and bluepoint LED eco devices from Hönle. It is not necessary to purchase new LED devices. The new optic is suitable for wavelengths of 365/385/405 nm. The focused light delivers an irradiation area of 10 mm x 1 mm and can achieve intensities of up to 7,000 mW/cm2. The light is distributed absolutely homogeneously across the irradiation field thanks to the special shape of the lens. The optic is particularly suitable for small-area applications where a particularly high intensity is required in a small space. This is necessary, for example, when curing in gaps. Adhesives dispensed in annular gaps can be cured quickly and reliably by arranging several LED heads in a circle around the circumference. The optimized curing and high intensity enable the shortest curing cycles for your process.
The bluepoint LED UV spotlight series from Hönle is especially suitable for curing UV adhesives in industrial assembly processes. The compact dimensions of the bluepoint LED head allow integration into the machine even where space is limited. The LED heads are passively cooled and require neither fans nor water cooling. As LEDs do not emit IR energy, curing takes place at low temperatures. This makes LED devices ideal for use with temperature-sensitive substrates.
Typical applications for bluepoint devices with the new lens include active alignment, rod lens or lens bonding in optics or medical technology, as well as underfills or securing SMDs on printed circuit boards in the electronics sector. For all these applications, UV adhesives from Panacol's Vitralit® series are also available that are specially adapted to the wavelengths of the bluepoint LED.
Read more about our Hoenle uv spotlights, the bluepoint series
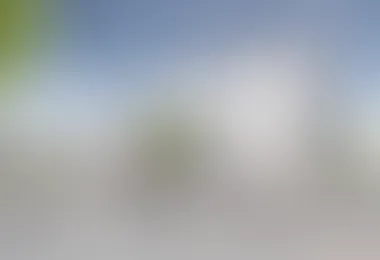
The new optic ensures particularly high intensities for UV adhesive curing in active alignment applications, for example
Structalit® 5859 is a new adhesive system developed by Panacol specifically for magnet bonding. This adhesive can be used for magnet/rotor bonding and for joining magnets in pole housings.
Structalit® 5859 is a one-component epoxy resin adhesive that cures at temperatures as low as 100°C. At 150 °C, the curing time can be reduced to as little as five minutes. The product has an impressively long open time and can be processed at room temperature for seven days.
Due to its high glass transition temperature (Tg) of 143 °C, Structalit® 5859 has a tensile shear strength of 17 MPa on steel − even at temperatures of 150 °C. In addition, the adhesive is characterized by high impact strength and good elongation at break, which makes it possible to use it with material pairings that have different coefficients of thermal expansion. Good gap bridging − to compensate for production-related tolerances −, resistance to aggressive contact media such as oil or coolant and excellent damping properties round off the diverse property profile of this new product.
Visit us from March 26-27, 2025 at COILTECH in Augsburg Germany, Hall 5 Stand G 28, to find out more about our latest adhesive developments.
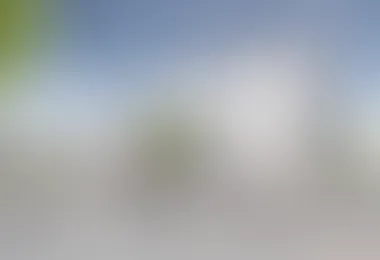
The magnets of an electric motor are attached with the Structalit® 5859 shown in blue
Read more about our adhesive solutions for magnet bonding
Panacol has developed a new UV adhesive specifically for foil lamination of organic (OPV) and perovskite-based (PSC) photovoltaic systems: Vitralit® UH 1411 is a very flexible, hybrid epoxy resin-acrylate adhesive that cures with UV light.
Vitralit® UH 1411 is a UV adhesive specially developed for sealing and bonding flexible PV modules. After application, Vitralit® UH 1411 can be cured by a combination of UV or visible light and heat, which enables precise curing even in potential shadow zones. Dr. Hönle's LED curing systems, such as the Powerline 820 HP AC IC, are particularly suitable. The modules of the Powerline can be stacked without gaps to completely irradiate the desired width. The intensity is adjustable and can be adapted to the web speed in the range of 10-100%, ensuring consistent curing results. The LED Powerline 820 AC IC HP is supplied and controlled either via the optionally available LED powerdrive IC or via an external power supply unit and customer-side control of the interface.
Once cured, the hybrid adhesive Vitralit® UH 1411 is very resistant to environmental and media influences, as well as being soft and flexible, thanks to its composition of epoxy resin and acrylate components. Vitralit® UH 1411 thus offers an optimized solution for the integration of flexible solar cells in modern indoor concepts.
A key advantage of Vitralit® UH 1411 is its high adhesion to all standard barrier foils and films used in the manufacture of flexible photovoltaic modules. The adhesive strength can be maintained even after high exposure to temperature and humidity. The adhesive is also transparent and non-yellowing, which ensures optimum light absorption and a long service life for the PV modules.
Organic and perovskite-based photovoltaic systems enable completely new applications both indoors and outdoors. The capture of artificial light indoors can be used to power wireless electronics. The flexibility of the new modules also makes it possible to attach them to geometrically challenging surfaces. The further development of adhesive technologies has made a decisive contribution to these advances. Panacol accompanies these developments by providing innovative high-tech adhesives that can be individually adapted to the relevant customer application.
Visit us from February 25-27, 2025 at the LOPEC in Munich, Stand B0 614 to find out more about our latest adhesive developments.
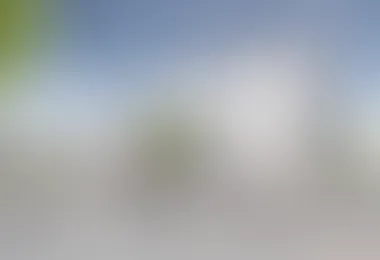
Vitralit® UH 1411 is applied to the barrier foil to seal the sensitive PV modules.
Panacol has developed Vitralit® UV E-2113, a new UV acrylic adhesive that is ideal for the rapid securing of commutators. This UV adhesive can be applied robotically and cures within seconds under UV light. The process of securing commutators can be greatly accelerated with Vitralit® UV E-2113.
Vitralit® UV E-2113 is a highly viscous and stable adhesive. Its optimized flow characteristics allow it to dispense easily into cavities. This adhesive has high adhesion to all metals: It adheres to the coil wires as well as to the solder joints and the commutator. The adhesive can be applied in a ring around the commutator in automated processes. Vitralit® UV E-2113 is a 1-component adhesive and does not require special handling during transportation, storage, and dispensing.
Vitralit® UV E-2113 cures in just a few seconds with light in the UVA range or in the visible range at a wavelength of 405 nm. Both traditional gas discharge lamps and LED systems can be used for curing. The curing of Panacol adhesives are optimized by the UV and LED UV curing systems from Dr. Hönle. For example, the Hönle high-intensity LED Powerline AC/IC HP systems will cure the Vitralit® UV E-2113 in seconds enabling high-speed, high-volume automated production. Fast, in-line light curing eliminates the need for lengthy and energy consuming oven processes. Commutator protection with Vitralit® E-2113 can significantly reduce production times and costs.
After curing, Vitralit® UV E-2113 has a dry surface and is highly resistant to vibration and impact. This adhesive creates low-stress bonds and temperature resistance in the range of -40 to 150°C which are typical requirements in the automotive industry.
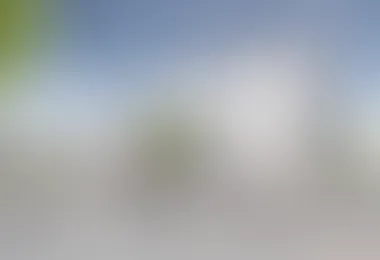
The new UV adhesive Vitralit® UV E-2113 protects the wires on the commutator
More info:
Download TDS of Vitralit® UV E-2113
Read more about our bonding solutions for e-motor assembly
Panacol will feature new optical grade resins for imprint and optical bonding applications at the SPIE Photonics West exhibition in San Francisco CA, USA from 28 to 30 January 2025. These new adhesives are typically used for light carpets in the automotive industry. They are also used in smart device sensors, wearables, and to create structured light in projectors or time-of-flight sensing applications, both for automotive and consumer products.
Panacol has successfully formulated resins for imprint replication of refractive lenses and diffractive optical elements (DOEs). These materials are highly suitable for micro- and nanoimprint lithography or wafer level optics. In addition to the suitability of these materials for commonly used glass wafers, the new generation products demonstrate outstanding adhesion to trending new polymer substrates including optical grade PET, PC or COP. Once applied and imprinted, the adhesives are quickly cured by UV light, creating a precise and durable structure. The optical properties are specifically tailored to meet the requirements of the targeted substrate.
One of the latest generation of optical materials, Vitralit® UC 1633, features a further improved yellowing resistance, higher optical transmission, and superior shape retention. Vitralit® UC 1633 is easy to demold from PDMS molds which makes it the perfect material to form microlenses such as those used in smart watches.
For unique optical applications and assembly, Panacol offers black UV-curable materials for shading and masking properties. “Black&Light” adhesives, such as Vitralit® BL UC 1103, can be cured in thicker layers by light only, resulting in optical densities of up to 6 (highly blocking). For assembly of optical components Panacol offers a wide range of UV curable adhesives for bonding and alignment. For curing in shadow zones dual cure adhesives with a secondary moisture or heat curing step are available.
These optical materials and adhesives for optical bonding are efficiently cured with high intensity LED curing systems from Hönle, which perfectly match the wavelengths of the Panacol photoinitiators. Once cured, Panacol’s optical grade adhesives are flexible and tension equalizing, reducing the stress on dissimilar substrates.
Visit us at our booth no. 4112 at the SPIE Photonics West exhibition in the Moscone Center in San Francisco CA, USA from 28 to 30 January 2025.
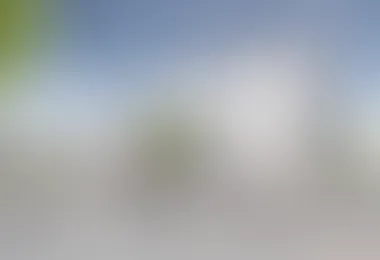
The new UV adhesive Vitralit® UC 1633 is used for microlenses on smart watch sensors
More info:
Download the TDS for Vitralit® UC 1633
Read more about our optical materials and adhesives for optical bonding
Perovskite-based and organic photovoltaic (OPV) cells represent a promising pathway to renewable energy generation due to their potential for lightweight, flexible, and potentially cost-effective solar power generation. Panacol complements new OPV technologies with Elecolit® 3648, a newly developed conductive adhesive. Elecolit® 3648 addresses one of the critical challenges in the commercialization and long-term reliability of organic solar cells: creating long-lasting, flexible electrical connections that create and maintain reliable electrical circuits.
Electronic components are typically connected by soldering. But solder materials are rigid and inflexible, and soldering temperatures are often too high for potentially heat-sensitive photoactive materials. Conventional conductive adhesives cure at lower temperatures but can still be brittle and inflexible.
This is why Elecolit® 3648 is a significant introduction. It is a very flexible, conductive adhesive. As it adheres well to plastics, including PI, PC, PVC, ABS, and FR4, Elecolit® 3648 is the perfect choice for an efficient attachment of wire leads and components to create flexible connections.
Elecolit® 3648 can be cured at relatively low temperatures of 80°C within a few minutes. At higher temperatures, Elecolit® 3648 can be hardened within seconds as a “snap cure” adhesive. As a one-component system, Elecolit® 3648 simplifies manufacturing processes by eliminating the need for mixing and therefore ensures a consistent application. It is easy to process and can be dispensed by conventional dispensing equipment, by jetting or screen printing.
Elecolit® 3648 can efficiently secure flexible resistors and create flexible electrical connections in solar cells to lead the generated electricity from the conductive tracks to the end device. This adhesive is also effective in touch sensors or wearable devices where flexibility is a desired property.
These features make Elecolit® 3648 the perfect solution to replace solder joints in applications subjected to vibration, oscillation or rapid temperature changes. This can includes all configurations of flexible electronics, and specifically OPV. As the adhesive maintains its integrity after repeated bending and stretching, Elecolit® 3648 can help to facilitate the development of new devices that withstand challenging operating conditions without losing performance.
Visit us from 23rd to 24th October 2024 at TechBlick in Berlin, Estrel Congress Center, Booth C03, to get more information about our latest adhesive developments.
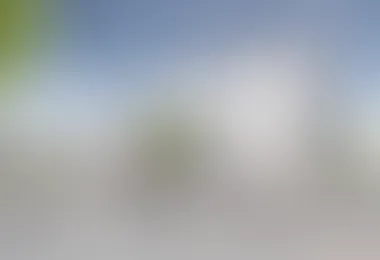
An electrically conductive adhesive is dispensed into laser-cut holes for the electrical connection of flexible solar films.
Download:
The international adhesives manufacturer Panacol joined the European Photonics Industry Consortium (EPIC) on July 1, 2024. EPIC is the world's leading industry association promoting the sustainable development of organizations active in the field of photonics in Europe.
Panacol has developed new optical resins and adhesives that are particularly suitable for photonics applications: For example, for optical materials used to create refractive lenses and diffractive optical elements (DOEs), micro- and nano-imprint lithography, wafer level optics and optical wafer bonding. These materials can be easily applied by puddle dispensing, spin coating or jetting. With excellent adhesion to common glass wafers as well as new polymer substrates (e.g. optical PET or PC) and very fast UV curing, a precise and durable microstructure is created. The new resins also meet the high optical requirements, such as resistance to yellowing, temperature and dimensional stability.
These resins are suitable for use in many companies that are also members of the EPIC association, allowing Panacol to make a valuable contribution to the technical success of a wide variety of photonic applications in the European market. At the same time, the large EPIC network, as well as the high-quality events organized by EPIC, represent a significant potential for Panacol to strengthen the awareness of its own brands and products and to open up new markets. Panacol will therefore take part in the planned EPIC delegation to Taiwan in September, and further activities within the consortium are already in preparation.
Together with other EPIC members along the value chain, Panacol plans to collaborate in the coming years to develop further complete technical solutions in order to jointly establish polymer optics on the market in a competitive manner suitable for mass production.
Read more on the EPIC homepage
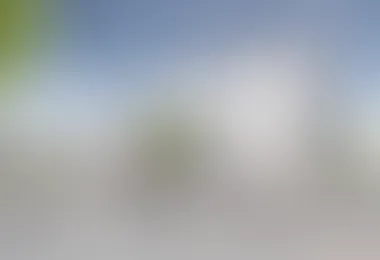
Special Panacol adhesives can be used as optical resins, for example to produce precisely shaped nano lenses
Panacol has developed a new epoxy resin adhesive specifically for bonding filters for oil, gas, and particle filtration. Structalit® 5826 VT is highly resistant to fluids and media and is very suitable for bonding filters used in shipbuilding and engine construction, exhaust gas purification systems, and the renewable energy industry.
Structalit® 5826 VT is a high-viscosity, one-component epoxy adhesive. High viscosity allows the adhesive to be applied easily between the filter and filter cap, as well as on the longitudinal seam of the filter fabric, without undesirable run-off. Despite its high viscosity, the adhesive effectively penetrates the filter fabric to create a strong, resilient bond.
Structalit® 5826 VT is cured thermally, requiring only a few minutes in an oven at 150°C. It can also be hardened with an induction curing process. With a temperature resistance of up to 200°C, this adhesive is suitable for use in a wide variety of liquid, gas or particle filters.
Epoxy-based adhesives generally possess higher resistance to environmental and media attack. Structalit® 5826 VT was created to be particularly resistant to oils and liquids. It has passed reliability testing in fluids according to DIN 53521 (70:30 Isooctan:Toluol); and passed oil resistance tests after 1000h aging.
All these characteristics make Structalit® 5826 VT the perfect choice for bonding oil, gas, and particle filters in many industries.
Download technical datasheet of Structalit® 5826 VT
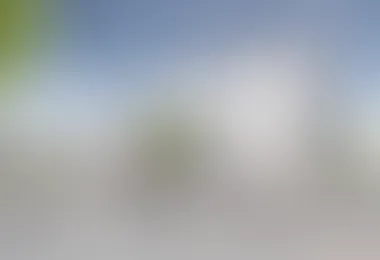
Epoxy Structalit® 5826 VT (here marked in blue) is used to bond a particle filter
At this year's CWIEME, from 14 to 16 May 2024 in Berlin, Panacol will be presenting the latest adhesives for the stress relief of wires on commutators, the bonding of magnets in electric motors, balance compensation in fan rotors and general bonding applications in the field of e-mobility and automotive electronics.
The UV adhesives in Panacol's Vitralit® range are particularly suitable for relieving stress on wires at the commutator. These adhesives are easy to work with. They can be applied to the wire/commutator connection and cured in seconds using UV light. The benefit of fast curing makes these adhesives the perfect solution for producing high volumes of commutators in short cycle times.
Newly developed, dual-curing (UV/moisture) adhesives are available for bonding magnets in electric motors. Despite the opacity of the magnet, UV curing the adhesive “squeeze-out” will tack and hold the magnet in place. The adhesive beneath the magnet, as well as in shadowed rotor pockets, will cure using atmospheric and surface moisture. All curing occurs at room temperature.
Panacol also offers a fast-curing acrylate adhesive for balancing fan rotors. This high density, UV adhesive can be jet dispensed into the balancing pockets of fan rotors. Balancing can be accomplished quickly and precisely without the use of metal weights. This process can significantly shorten production cycle time and significantly reduce component rejects.
The UV devices from Dr Hönle, also being presented at CWIEME, are well suited for curing Panacol’s UV adhesives. These UV and LED curing systems provide intensity and wavelength options that can optimize any bonding process. A complete bonding solution from a single source!
Panacol will also be showcasing its full portfolio of adhesives for various automotive bonding applications at CWIEME. Adhesives are available for battery cell sealing, PCB component attachment, optical alignment, and sensor potting.
Visit us at our stand 12 B 33 in hall 1.2 at CWIEME from 14 to 16 May 2024 in Berlin!
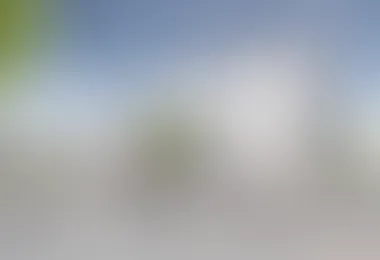
A modern car or EV contains numerous electronic components and assemblies that require attachment, encapsulation, and coating with high-tech adhesives and sealants.
Download:
High-tech Adhesives for E-Mobility and Automotive Electronics
Panacol presents its first series of new, UV curable, black epoxy resin adhesives. These “Black&Light” adhesives, Vitralit® BL UC 1101, Vitralit® BL UC 1102 and Vitralit® BL UC 1103, can be cured in thicker layers using only UV light, eliminating the need for a secondary curing mechanism. Another major benefit from those Black&Light adhesives is room temperature shipping and storage. Conventional single-component, black-colored epoxy adhesives must be transported and stored cold or deep-frozen.
The black color in a conventional UV adhesive absorbs a high percentage of the UV curing energy. This means that the UV light energy required to fully polymerize an adhesive only penetrates a few micrometers. This phenomenon leads to the formation of a superficial “skin”, while the adhesive underneath remains uncured. The new black Vitralit® BL UC adhesives from Panacol can be cured to greater than 1mm in thickness, purely with UV LED light. UV LED curing systems from Dr. Hönle are perfectly matched to the absorption wavelengths of the Black&Light technology, ensuring optimal curing of the black adhesives.
Vitralit® BL UC 1101, Vitralit® BL UC 1102, and Vitralit® BL UC 1103 are Panacol’s new Black&Light adhesives and they cover a wide range of applications. They are suitable for component encapsulation, glob top, or edge bonding in electronics production. They can also be used as optical adhesives in applications requiring high OD (optical density) values.
Vitralit® BL UC 1101 is the perfect choice if a thick layer of adhesive is needed. It cures reliably in thick layers up to 1.3 mm, resulting in an optical density of up to 3.9. If a high optical density in lower layer thickness is needed, Vitralit® BL UC 1103 with OD values of up to 6 is the best option. In optoelectronic component assembly, Vitralit® BL UC adhesives minimize reflections and can safeguard the sensitive transmission values required for automotive sensors.
All three new adhesives offer outstanding mechanical properties including high glass transition temperatures, low shrinkage, and low coefficient of thermal expansion. Those characteristics ensure reliable bonding results with an excellent thermal and positioning stability. As the Black&Light technology is compatible with many Vitralit® epoxy resin adhesives from Panacol, individual adhesive solutions matching specific curing conditions and/or mechanical properties are possible.
Download the technical datasheets of:
Read more about our new Black&Light adhesives
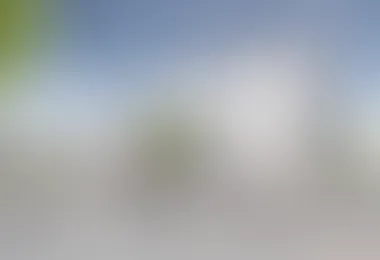
Black epoxies are being cured with UV LED light
Video:
Flexible electronics manufacturers are pushing traditional boundaries such as volumetric form factor, functionality, and design flexibility in consumer electronics. To this end, Panacol and Hönle UV Technology have successfully developed turnkey solutions comprising of multi-functional adhesives and UV curing equipment, that can be tailored for novel Photovoltaic and flexible electronics applications.
For OPV applications, these new UV and UV-LED curable adhesives were developed specially for laminating barrier foils. They provide higher resistance to environmental stresses, an improved compatibility to the PV material and low WVTR (Water Vapor Transmission Rate). Being UV-curable, these adhesives offer high throughput processes, including roll-to-roll that can be run with greater efficiency reducing total cost of ownership. The adhesives requirements such as flow properties can be modified in this context to suit the application process perfectly.
Flexible and bendable uv adhesives have also been created for more traditional applications that are now being performed on flex circuits. They include new underfills for die-attach as well as structural adhesives for component edge bonding. All uv adhesives from Panacol get easily cured with high intensity UV and/or UV-LED curing systems from Hönle, which perfectly match the wavelengths of the Panacol photoinitiators. Their light footprint options range from 3 mm diameter spot units to linear LED arrays that can exceed one meter in length, making it the perfect choice for smaller and larger irradiation areas.
The latest conductive adhesives from Panacol can efficiently secure flexible resistors and create flexible electrical connections in solar cells, touch sensors and wearable devices. This includes a one-component, silver-filled conductive adhesive that adheres very well to plastics, including polyimide, PC, PVC, ABS, and FR4 boards. When fully cured, the adhesive is very flexible with high peel strength, making it the perfect choice for use in applications subject to vibration, oscillation or rapid temperature changes. A major advantage is its very easy handling and storage as it only needs to be stored refrigerated, not frozen. It is easily dispensed, and cures within minutes at temperatures as low as 100°C. This makes it possible to fixture semiconductors and create electrical connections in a single step.
The specific requirements of the application and its assembly process are key factors to consider when making an adhesive selection. Significant benefits can be realized when component design assembly, adhesive properties, and the curing process (UV or thermal) are precisely coordinated. Panacol works closely with manufacturers in all facets to assist in creating an optimized bonding process. This results in increased efficiency and reduces total operational costs.
Visit us at Lopec, the International Exhibition for Flexible, Organic and Printed Electronics in Munich/Germany. From 6th to 7th March 2024, you find us in Hall B0, Booth 614 and get more information about our latest adhesive developments.
Read more about our adhesives for photovoltaics
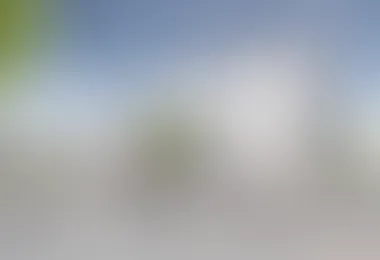
Flexible adhesives are used for foil lamination, electrical conductive bonding, underfills, edge bonds and SMD fixation on a flexible PCB and OPV cell
Download Flyer:
Panacol will feature new optical grade resins and adhesives for imprint and optical bonding applications at the SPIE Photonics West exhibition in San Francisco CA, USA from 30 January to 1 February 2024. These new adhesives can be used for light carpets in the automotive industry, for sensors in smart devices and wearables, or for creating structured light in projectors or time-of-flight sensing applications.
Panacol specially formulated adhesives for imprint replication of refractive lenses and diffractive optical elements (DOEs). These adhesives are suitable for micro- and nano-imprint lithography, wafer level optics, and wafer bonding. The newly introduced adhesives Vitralit® UC 1632 and Vitralit® UC 1658 are in the viscosity range of 100 to 200 mPas and can thus be easily applied via puddle dispensing, spin-coating or jetting. They offer excellent adhesion to commonly used grades of glass wafers and upcoming new polymer substrates including optical grade PET or PC. Once applied and imprinted, the adhesives are quickly cured with UV light, creating a precise and durable structure on the wafer. Both adhesives are tailored specifically to meet the high demands of optical reliability, such as low yellowing, temperature stability, and shape retention.
For black shading and masking purposes, Panacol also offers a black UV curable adhesive, Vitralit® BL UC 1103. This black epoxy adhesive is permeable to UV light while uncured. After curing it is opaque and light blocking.
For optical bonding and alignment, Panacol has developed UV curable adhesives Vitralit® 7311, Vitralit® VBB-60, and Vitralit® 1860, as well as heat curable adhesives Structalit® 5531 and Structalit® 5511. These adhesives feature high adhesion to glass and widely used plastic substrates. Adhesive Vitralit® UD 8057 is formulated for dual curing using UV/visible light and atmospheric moisture. This allows the adhesive to complete its curing using moisture in shaded areas that cannot be reached with UV/visible light.
These adhesives for optical bonding get easily cured with high intense LED curing systems of Hönle, which perfectly match the wavelengths of the Panacol photoinitiators. Once cured, Panacol’s optical grade adhesives are flexible and tension equalizing, reducing the stress on dissimilar substrates.
Visit us from 30 January to 1 February 2024 at SPIE Photonics West at the Moscone Center in San Francisco, California/USA, at our stand number 4342!
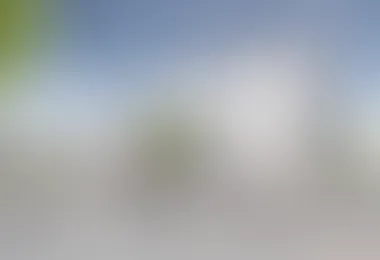
An epoxy resin adhesive is used as imprint material for nano structures on a glass wafer.
Download Flyer:
Organic photovoltaics (OPV) and Perovskite-based systems are creating radically new applications in consumer electronics. They include indoor light harvesting to extend battery life of wearables, and outdoor energy generation with performance in regard of their flexibility previously unimaginable from conventional photovoltaics. The same is true for flexible electronics. A key contributor to these advancements has come from progress in bonding technologies. Panacol accompanies these developments by providing high tech adhesives that elevate flexible photovoltaics to the next level.
Today’s adhesives go beyond the basic benefits of sound structural bonding by providing additional functionality to the assembly. Panacol has successfully developed a range of multi-functional adhesive selections for applications in flexible photovoltaics and electronics. For OPV applications, these adhesives provide higher resistance to environmental stresses, an improved compatibility to the PV material and a good adhesion to the substrates. New conductive adhesives efficiently adhere and protect electrical connections for SMD components in flexible assemblies.
In all cases, the specific requirements of the application and its assembly process are key factors to consider when making an adhesive selection. Significant benefits can be realized when an optimal pairing is achieved with the component design, assembly, (UV) adhesive properties, and the curing process. High throughput processes, including roll-to-roll can be run with greater efficiency which reduces total cost of operation. The adhesives requirements such as flow properties can be modified in this context to suit the application process perfectly.
As new designs are evolving rapidly, very little standardization exists in the manufacturing of OPV. To support this evolution, adhesives must be modified or developed to meet the customers’ unique OPV design, materials, and processes. Panacol has anticipated this need and is prepared to work with manufacturers to provide adhesive customization and development as quickly as possible.
Visit us from 17th to 18th October 2023 at TechBlick in Berlin, Estrel Congress Center, Booth F4 to get more information about our latest adhesive developments.
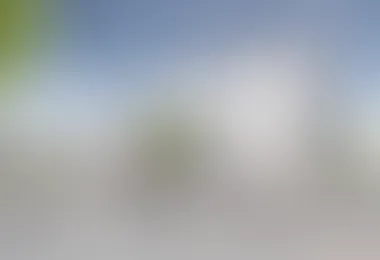
Adhesives are applied on barrier foil to seal the delicate OPV modules.
Download Flyer:
Wearable patient monitoring devices are worn directly on the body and are being used in increasing numbers. These devices include diabetes sensors for monitoring blood glucose levels (GCM), as well as wireless monitors that transmit patient information to healthcare providers. They must be reliable and durable, while also safe for direct skin contact. Panacol has developed a broad portfolio of specialty adhesives for this purpose that meet the stringent demands imposed by medical device manufacturers. To be able to provide a complete bonding solution, Panacol teamed with metering equipment manufacturer Scheugenpflug and UV equipment manufacturer Dr. Hönle. A system concept was identified and successfully tested that enables precise metering for the dispensing of low volumes of UV adhesives with integrated LED UV curing.
Panacol’s medical device adhesives exhibit excellent adhesion to commonly used medical-grade substrates, including polycarbonate, polyimides, polyamides, stainless steel and ceramic. These adhesives are tested for biocompatibility in accordance with ISO 10993-4/-5/-10/-23 and/or USP Class VI protocols.
This group of adhesives includes LED curable UV acrylates and UV epoxies which provide the shortest curing cycle times for high volume production. They are ideal for needle/hub assembly, component attachment, and for sealing enclosures. Multiple viscosity ranges are available to provide the best match to component configuration and assembly process. Fluorescing versions are available to enhance quality control relying on in-line vision systems.
Also included in this group are electrically conductive adhesives and conventional thermosetting epoxies. They offer connectivity and attachment solutions for PCB and electrical component assembly. Several epoxy selections are available with high ionic purity which is essential to minimize the risk of corrosion on the PCB. Panacol’s silver-filled electrically conductive adhesives can often replace solder joints or be applied on bendable or flexible wearables.
Accurate and consistent adhesive dispensing is mandatory when assembling medical devices. For the small dispensing volumes, the best choice is the high-precision DosPL DPL2001 micro dispensing head from Scheugenpflug, Part of the Atlas Copco Group. This allows highly accurate application of the adhesives even for the smallest volumes down to the µl range. This allows glob tops to be reliably set to 0.003ml, dispensing accuracies of less than 0.5% to be achieved, and the thinnest lines to be made on the plastic housing with precise start and stop.
The dispensing head works on the principle of volumetric dispensing. A control system reliably detects viscosity fluctuations and ensures consistently high precision of the bonding contour.
The curing or hardening of Panacol’s UV acrylate and epoxy adhesives can be achieved in seconds due to their uniquely formulated compositions. LED curing systems from industry leader Dr. Hönle enable maximum optimization of the curing process. This ensures the shortest curing cycle time and the highest thruput. In the tested system concept, Hönle's LED Spot 40 IC, with a wavelength of 405nm was used. The compact design of this LED head allowed it to be integrated with the DosPL DPL2001 dispensing head into Scheugenpflug’s DispensingCell DC803 multifunction robotic cell. This work cell permits components to remain in one position for both dispensing and UV curing processes. Parts handling is minimized, along with the risks of component movement, contamination, and adhesive migration. This integrated system concept ensures the adhesive bonding process is performed to the highest quality standards with the greatest efficiency. Whether batch production or continuous flow, integrated adhesive bonding systems from Panacol, Scheugenpflug, and Hönle meet the demanding production requirements for medical wearables.
Read more about our Medical Grade Adhesives
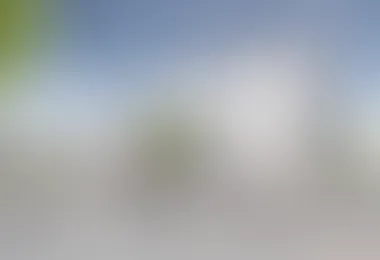
Medical grade adhesives contribute to design flexibility and fast assembly of monitoring sensors.
Watch the video:
At the BondExpo fair in Stuttgart Panacol will present its new Structalit® 5604. It is an extremely fast-curing adhesive which is specifically developed for bonding SMDs to printed circuit boards. The adhesive is based on epoxy resin and is, despite its high viscosity, suitable for jet application.
Structalit® 5604 is a one-component epoxy resin adhesive that contrasts well with green PCB material due to its red color. This makes it possible to ensure visual inline inspection. The one-component adhesive can be dispensed in production through jetting, valve dispensing or screen printing. Its ideally adjusted viscosity and high thixotropy index enable high-speed dispensing, precise dot profiles, and non-slumping wet adhesion prior to curing.
This adhesive is cured with heat. The thermal cure occurs within minutes, even at low temperatures. When fully cured, the adhesive is extremely temperature resistant. It can withstand short-term temperatures of up to 270°C, making it suitable for reflow soldering processes.
Structalit® 5604 is particularly shock-resistant and durably adheres to FR4 printed circuit boards, metals, and epoxy-based molded materials. Due to its high glass transition range of >115°C, the adhesive is ideal for electronic component assembly. It does not lose adhesion or softens at elevated temperatures. As Structalit® 5604 was developed specifically for use in electronics, it has high ionic purity and thus provides optimum protection against internal corrosion.
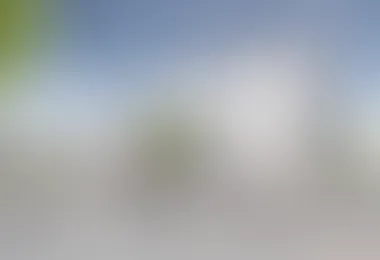
The red Structalit® 5604 is ideal for fixing SMDs and electronic components. Its red color contrasts well against green PCBs.
With the introduction of Vitralit® UD 8055 and Vitralit® UD 8056, Panacol continues to expand its portfolio of dual-curing acrylic adhesive systems. These adhesives principally cure with UV light. They also possess a secondary moisture post-cure mechanism to compensate for shadowed areas. A special characteristic of these two adhesive systems is their high glass transition range of over 100°C, which helps to preserve high-strength bonds through thermal cycling stress.
Vitralit® UD 8055 and Vitralit® UD 8056 are ideal for use as encapsulants that provide environmental protection to sensors and PCB components. They can also be used for bonding dissimilar substrates including many plastics and metals where undercuts or geometry-related cavities are present. This is precisely where they demonstrate their dual-cure advantage. The secondary moisture cure mechanism overcomes the challenge of shadowed bond lines and ensures a reliable bonding process.
In the primary UV curing process, the bonded areas in the component are fixtured in seconds by UV light. LED curing systems can be used possessing wavelengths of 365 or 405nm. LED systems do not require any warm-up phases and thus enable the shortest cycle times. LED and UV pioneer Dr. Hönle offers a broad selection of spot and flood-style systems that are optimally matched to Panacol's adhesives and can be individually adapted to the application requirements.
In the secondary post-curing process, uncured monomers crosslink in shadowed areas by atmospheric moisture without stress and the need for secondary thermal exposure. This technology enables fast cycle times and high-volume production without subjecting temperature-sensitive electronics or components to excessive thermal stress.
A high glass transition range (Tg) is particularly important when encapsulations and bonded substrates must withstand thermal stress over long periods of time. Exceeding 100°C, the Tg of Vitralit® UD 8055 and Vitralit® UD 8056 ensures that thermal expansion coefficients behave homogeneously in the application area. This prevents the adhesive from losing bond strength and creating excessive stress between components which can lead to delamination or cracking in the electronics. Vitralit® UD 8055 and Vitralit® UD 8056 were primarily developed for the production of sensors, PCBs and flex PCBs that are used in consumer and automotive electronics. These components are usually designed for use up to 100°C, making acrylate systems with a Tg above 100°C the ideal solution for such applications.
Vitralit® UD 8055 and Vitralit® UD 8056 achieve high adhesion with typical substrates such as FR4, PC and PBT. Vitralit® UD 8055 has demonstrated very reliable adhesive performance through challenging 85/85 aging tests. Vitralit® UD 8056 is particularly impressive for its performance on LCP and has passed UL94 HB tests. With depth of cure that exceeds several millimeters, these two low-halogen adhesives can be used in a wide range of electronic assembly applications.
Download TDS: Vitralit® UD 8055 and Vitralit® UD 8056
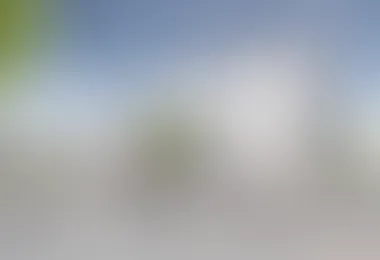
Vitralit® UD 8055 - shown here in blue - is cured as connector encapsulation with Hönle's bluepoint LED; the curing of the shadowed area under the connector is achieved by moisture post-curing.
International adhesives manufacturer Panacol is the newest member of ACOP (Aachen Center for Optics Production) as of December 2022. ACOP, based in Aachen, Germany, is an initiative of the Fraunhofer Institute for Production Technology (IPT), with the aim of promoting cooperation between researchers and industry in the field of optics. As a member of ACOP, Panacol joins an expert group of companies that convene to develop sustainable solutions for the manufacturing of optics and optical devices. This includes conceptual design, mold making, metrology, as well as all the developmental steps from first generation prototypes to series production with all required documentation.
Immediately upon becoming a member, Panacol became involved in project discussions, contributing its expertise in the field of adhesives and bonding technology. The project discussions typically involve the traditional use of adhesives as composite materials for optical assembly. However, project work can also be less conventional, such as using liquid adhesive formulations to produce polymer optics. The projects and discussions can be extremely diverse. One project, for example, is concerned with transferring the expertise of glass molding process simulation to bonded optical systems in order to predict characteristics such as shrinkage behavior or other mechanical and optical parameters or to be able to better estimate their influence. Another project identifies suitable cleaning methods for the pre-treatment of optical systems prior to subsequent processing and assembling.
Particularly in the area of free-form optics with liquid polymers, Panacol sees an enormous variety of possibilities for product and production variants. Products from consumer electronics and sensor technology offer much potential for MLAs (Micro Lens Arrays), DOEs (Diffractive Optical Elements), and meta lenses, (i.e. optical components that do not focus light like conventional lenses but are based on nanostructured surfaces). Increasingly smaller designs, more homogeneous signal pickup and distribution contribute enormously to increased performance potential in such applications. However, it is essential to understand and master the overall object or the entire manufacturing chain. The diversity of the partner companies, the open technical discussions, and the resulting synergies that are created greatly benefit each member company. Greater knowledge and new lines of thinking can be applied toward manufacturing technology and the metrology of optical systems.
Panacol has the ability to utilize these new concepts and ideas to assist manufacturers with their own product and process improvements. Together with the other ACOP members in the value chain, Panacol is planning to move forward with proposals that can jointly introduce competitive polymer optics into the market that are suitable for mass production.
About ACOP
The ACOP partner community is an R&D network platform with currently 14 industrial partners and the Fraunhofer Institute. It conducts collaborative R&D in the field of optics production in the context of digital and physical networking. The focus of the collaborative R&D is on pre-competitive topics with a large overlap of interests among the ACOP industrial partners, enabling a highly synergetic use of R&D investments.
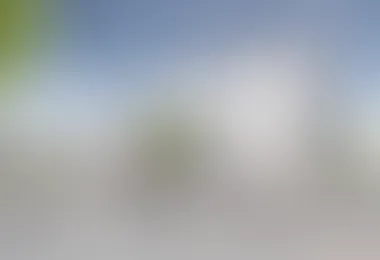
Adhesives are used, for example, in the production of plastic lenses
(Photo: Fraunhofer IPT)
With the new "Black&Light" adhesives, Panacol has developed a new adhesive technology: deep curing black epoxies. Black epoxy adhesives from Panacol's Vitralit® product range can now be cured with UV light sources in thicker layers, without resorting to secondary curing mechanisms.
Conventional black UV adhesives have a major disadvantage: the black color absorbs a high proportion of the UV intensity, which means that the energy needed to fully polymerize an adhesive can only penetrate a few micrometers. This results in surface “skin” formation on black adhesives, but not a complete cure. They must then be cured in a secondary thermal curing process at temperatures above 100°C.
Panacol's new "Black&Light" technology enables the complete curing of black epoxy adhesives with LED UV energy. Depth of cure can range from a few hundred micrometers to several millimeters. The adhesives are suitable for encapsulation, glob top, or edge bonding in electronics manufacturing, as well as for optical adhesive systems where high OD values (optical density) are required. They are suitable for optoelectronic applications to help minimize reflections and enhance sensor transmission values.
A typical manufacturing process using "Black&Light" technology can be as follows: The black adhesive is dispensed and cured with the appropriate wavelength and intensity. During the curing process, the “Black&Light” technology within the adhesive enables the UV rays to penetrate and complete a full cure. Once the adhesive polymerization is complete, the structure of the "Black&Light" technology prohibits light transmission, resulting in a fully cured adhesive system that remains irreversibly black.
The "Black&Light" technology is compatible with many Vitralit® epoxy adhesives from Panacol. Custom adhesive solutions can be created to accommodate unique requirements for amount of light blocking and depth of cure. The "Black&Light" adhesive systems can be very specifically adapted to specifications of the respective application.
Another major advantage of the "Black&Light" adhesives is storage. Many single-component, black epoxies require deep frozen transportation and storage. The "Black&Light" epoxy adhesives can be stored and shipped at room temperature or under normal refrigeration.
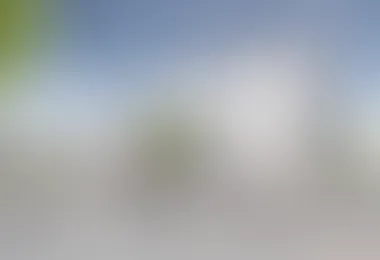
A black epoxy coating is being cured with UV LED light
Video:
Panacol has developed Vitralit® UD 4292 F, a new dual-curing adhesive that cures primarily by UV light with a secondary anerobic cure for shadowed areas. The special feature of this adhesive system is the high glass transition range of >130°C when cured under optimum conditions.
In response to a growing market demand for UV anerobic adhesive systems, Panacol has expanded its portfolio of dual-curing adhesive systems with Vitralit® UD 4292 F. This new product is ideally suited for structural bonding and sealing in automotive and electronics applications.
Vitralit® UD 4292 F is a transparent acrylic adhesive that cures in just a few seconds with light in the UVA or visible range. LED curing devices from Dr. Hönle provide light curing energy in wavelengths and intensity that optimize absorption by the adhesive’s photoinitiators for highly efficient UV light curing cycles. In shadowed areas, this adhesive reacts with metal ions in the absence of oxygen to ensure full cure. The secondary anerobic curing can be accelerated by adding heat or by applying a chemical activator to one of the surfaces to be bonded. When properly cured, Vitralit® UD 4292 F exhibits very high pull-out forces on various metals.
These properties make Vitralit® UD 4292 F particularly desireable for a wide variety of electric motor assembly applications, including structural bonding of ball bearings or shaft-hub connections on rotors and stators. The high glass transition temperature of over 130°C ensures that the adhesive system retains its bond strength under temperature fluctuations and dynamic stress. This UV anaerobic adhesive system meets the demanding assembly requirements in the electric motor and electric vehicle (EV) markets.
For visual process control, the composition of Vitralit® UD 4292 F contains a fluorescent marker that glows bright blue when exposed to low intensity UV light, making it visible in very thin gaps.
Download TDS: Vitralit® UD 4292 F
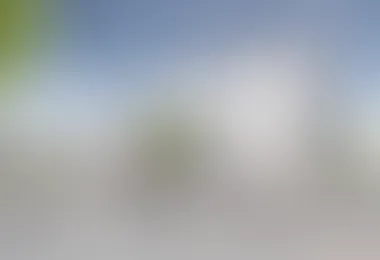
Vitralit® UD 4292 F is particularly suitable for metal bonding where all areas cannot be reached by UV light (shown in light blue in the picture).
Steinbach/Taunus, 28 June 2022
Panacol introduces new line of masking materials
Panacol has developed new UV curable masking materials for industrial processes. These masking materials are part of the Vitralit® MASK product line. They can be easily applied, cured in seconds by exposure to UV light, and then removed by a simple peel, or for those masks with higher adhesion, hot water dip and peel.
UV mask material is typically used in high value component fabrication that involves processes for surface enhancement. These processes may include acid cleaning, grit blasting, or shot peening. Component surfaces or internal cavities may need to be insulated from these processes for reasons of functionality. Masking materials are applied as temporary barriers, that are subsequently removed from the completed component after processing. Typical applications include the manufacture of turbine components, orthopedic devices or prosthesis, and other industrial component processes such as the coating of circuit boards and plastics.
The UV masking material is derived from light curable adhesive technology. Panacol’s family of UV light curable mask materials are solvent-free and can be easily applied and cured in seconds with a UV light source. The curing system may be broad spectrum UV or LED in in wavelengths of 365 or 405nm.The uncured liquid mask can be applied on components by syringe, dip, or spray. The masks are available in many viscosities to accommodate a wide variety of component configurations and applications. Both high and low viscosity masks from Panacol can be easily dispensed through spray valves onto larger surfaces. All Vitralit® MASK materials provide uniform and consistent protection from high impact particulates, hot acids, alkali solutions, plating, and paint. Vitralit® UV masks are available in green color to provide higher contrast for better visual inspection.
Removal of Panacol UV mask materials such as Vitralit® MASK 20107 or 20109 is accomplished by a simple peel, or a hot water dip and peel. A selection of Panacol UV masks, such as the new Vitralit® MASK 20116, have extremely high surface adhesion for the most rigorous processing. These UV masks are best removed through incineration. Panacol UV masking materials do not leave surface residue after peeling or incineration.
More about UV-Masks
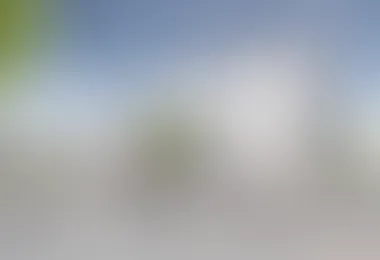
The green colored Vitralit® MASK 20117 was applied to a metal alloy prosthesis to protect parts of the surface from grit blasting.
Panacol launches new reworkable edge bonding adhesive
Panacol has developed Structalit® 5705, a new, removable edge bonder specifically formulated for bonding consumer electronics components. In addition to reworkability, the main feature of the black adhesive is that it fluoresces yellow when excited by UV light. This significantly enhances the accuracy of in-line optical inspection systems.
Edge bonding adhesives are used to quickly secure electronic components to printed circuit boards. This fastening method offers superior protection from shock, vibration, and thermal stress. As a constructive alternative to underfill processes, edge bonding increases the impact and bending strength of BGAs and other chip packages. Edge bonding can also be preferable to underfills when flux residues are present on PCB and component surfaces.
Structalit® 5705 is a black, thermosetting epoxy resin adhesive that is characterized by its viscous flow properties and high thixotropy index. These properties enable precise placement of the adhesive with no subsequent migration. Structalit® 5705 may be dispensed using pneumatic valves, or through highly efficient, contactless jet dispense systems. This epoxy resin-based edge bonder is low in halogens, and is ideal for electronic components assembly.
A typical feature of PCB adhesives is a black coloring that is used for light blocking and concealment. Visual inspection of edge bond placement is commonly performed by manufacturers using in-line camera systems. Dark-colored, low contrast chips often present difficulties for precise optical measurement. Panacol solves this problem by incorporating a yellow fluorescence into the black Structalit® 5705. The fluorescence is excited by short wavelength light, for instance 365nm. The highly contrasting fluorescence makes it easier for manufacturers to perform in-line inspections, resulting in faster parts processing and increased throughput.
For manufacturers of electronic components, a new challenge is becoming increasingly important. Global environmental associations are successfully lobbying for legislation to minimize electronic waste. A critical step in this sustainable strategy is the ability to rework and repair individual modules on printed circuit boards. Reworkability and repair reduces the amount of electronic component scrap that must be disposed into the environment. Structalit® 5705 from Panacol provides a reworkability feature. The adhesive can be removed without damaging the bonded components. This enables faulty components to be removed, and repaired after assembly.
Structalit® 5705 edge bonding adhesive is selectively reworkable when the cured adhesive receives thermal exposure above its glass transition temperature (Tg) of 150°C. The adhesive softens, and can be manually scraped away using a small spatula or similar instrument. It is only above this critical temperature threshold that the product becomes workable. Below this temperature, Structalit® 5705 protects bonded components with reliable bond strength and consistent performance.
Another pressing need for the reworkability of bonded components stems from the current global supply chain parts shortages. Automotive and consumer electronics sectors are experiencing massive production delays, primarily from a shortage of integrated circuits (chips) and electronic board components. The ability to rework components can help to mitigate some of these shortages. Reusing components not only offers advantages for the environment, but has also become essential for maintaining current production processes caused by supply chain bottlenecks.
Structalit® 5705 edge bonding adhesive can be used in conjunction with Panacol’s reworkable underfill, Structalit® 5751. Both adhesives can be applied wet-on-wet and cured together in just one oven process step. The reworkability of both adhesives provides manufacturers with the means to repair components after assembly, and reduce electronic waste.
Download technical datasheet of Structalit® 5705
Read more about Panacol bonding solutions for SMD assembly
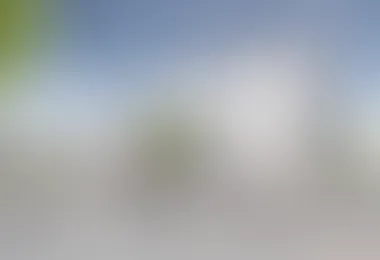
Black edge bonding adhesive Structalit® 5705 fluoresces brightly yellow under uv light.
Steinbach/Taunus, 21 February 2022
New epoxy adhesive offers maximum protection for potting applications
Developed by Panacol, Structalit® 5801 is a new 2-component adhesive system that demonstrates exceptional chemical and moisture resistance after accelerated aging. This resistance makes Structalit® 5801 an ideal material for the structural bonding and potting of electronic components that require the highest level of environmental protection.
Structalit® 5801 is a black, 2-component epoxy adhesive system with a simple 2:1 mixing ratio. Curing takes place within 12 hours at room temperature. For faster processing, this adhesive can also be cured thermally, in as little as 30 minutes at a moderate temperature of 80°C. Lower temperature curing minimizes thermal stress on components, and the shorter cycle time improves productivity. This medium-viscosity adhesive blend has excellent adhesion to metals including aluminum and stainless steel. It is well suited for the structural bonding of metal frames and housings. Structalit® 5801 also exhibits very good adhesion to plastics, such as PA6 GF or PBT. This multi-substrate adhesion allows Structalit® 5801 to be used for many material combinations typically found in the consumer and automotive electronics industries.
This newly developed adhesive cures with low shrinkage, and exhibits good vibration and shock resistance due to its high bond strength and unitizing properties. During aging tests at temperatures above 130°C, Structalit® 5801 actually gains bond strength. Adhesive exposure to transmission oil, biodiesel, and alcohol during aging resulted in minimal loss of bond strength. This is mainly due to the high degree of crosslinking and the low moisture absorption of this adhesive.
Structalit® 5801 can be dispensed from a 50 ml dual-chamber cartridge which is ideal for manual, short-run, or semi-automated production. This epoxy system is also available in sedimentation-stable bulk containers which can be used with meter-mix equipment for high volume production.
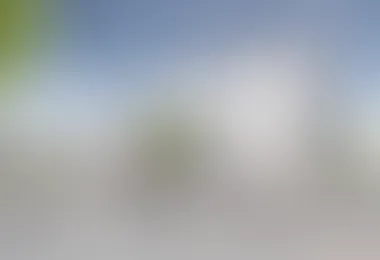
Structalit® 5801 is applied as potting to protect printed circuit boards in enclosures.
Steinbach/Taunus, 10 December 2021
Flexible Conductive Epoxy from Panacol
Elecolit® 3647 is a new addition to Panacol’s extensive portfolio of electrically conductive epoxy systems. With a history of demonstrated success, this silver-filled conductive adhesive is particularly suitable for bonding with temperature-sensitive films or flex PCBs.
Elecolit® 3647 is a one-component, silver-filled conductive adhesive that adheres very well to plastics, including polyimide, PC, PVC, ABS, and FR4 board. When fully cured, the adhesive is very flexible with high peel strength, making it the perfect choice for use in applications subject to vibration, oscillation or rapid temperature changes. Elecolit® 3647 can be used for die attach applications and component assembly on flexible films and printed circuit boards. This conductive adhesive has utilization in printed and “in-molded” electronics, wearables, and the conductive attachment of semiconductor chips.
A major advantage of Elecolit® 3647 is it’s very easy handling and storage. The adhesive only needs to be stored refrigerated, not frozen! The single-component adhesive can be dispensed, and cures within minutes at temperatures as low as 100°C. This makes it possible to fixture semiconductors and create electrical connections in a single step.
Read more about our portfolio of electrically conductive adhesives
Download the technical datasheet for Elecolit® 3647
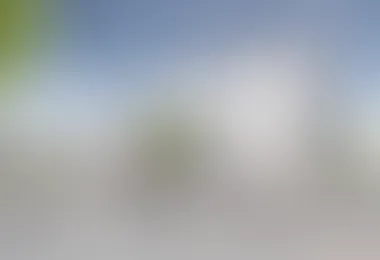
Bonding and contacting in one step: Small chips are fixed to flexible tracks with a conductive connection using Elecolit® 3647
Steinbach/Germany, 20 September 2021
New Panacol epoxy adhesive for bonding magnets
Structalit® 5858 is a modified, one-component epoxy resin adhesive that was developed specifically for bonding magnets into electric motors. Its high bond strength and impact resistance ensures reliable bonding.
Structalit® 5858 can be cured thermally in a conventional oven at temperatures from 100°C. It is also possible to use induction curing for faster polymerization and shorter curing cycles. The adhesive requires storage between 0-10°C, but its stable viscosity and reactivity allow it to be processed on the line at ambient temperature for up to seven days.
The Structalit® 5858 was developed by Panacol to expand its line of adhesives for electric motor assembly. After proper curing, Structalit® 5858 generates excellent adhesion to metals. With bond strength over 34 MPa on steel and aluminum, this adhesive creates reliable and high-strength bonds. Even at temperatures above 100°C, Structalit® 5858 continues to exhibit excellent superior bond strength, ensuring consistent performance during thermal stress. The high impact strength of this modified epoxy ensures that bonded components will not loosen or separate from operational vibration or external forces. Structalit® 5858 is particularly suitable for bonding magnets, such as the connection of half-shell magnets in stators, or permanent magnets on rotors.
Download the technical datasheet for Structalit® 5858
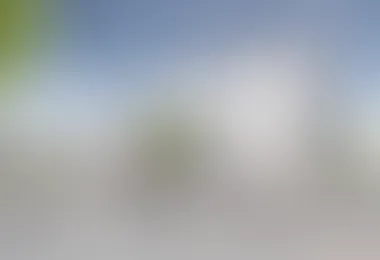
The adhesive marked in light blue shows exemplary magnetic bonding with Structalit® 5858 in an electric motor.
Steinbach/Germany, 2 August 2021
New biocompatible UV adhesive for soft plastics
Panacol has developed a new plastic bonder that is certified to USP Class VI biocompatibility standards for medical device assembly applications. Vitralit® UV 7030 features high elongation at break, excellent adhesion to difficult-to-bond plastics, and rapid curing under UV light.
The various material selections and pairings of flexible tubing and rigid connectors often create significant assembly challenges in high volume production. Materials used to create infusion lines, catheters, and similar medical devices may include TPU, TPE, PEN, polyamides, Pebax®, polycarbonate, ABS and PEEK. These thermoplastics and thermoplastic elastomers provide many desirable properties, but some combinations can be difficult to bond. After assembly, these materials are challenged by torsional stresses at the points of transition between the soft tubing and the hard connector. Panacol developed the adhesive Vitralit® UV 7030 to specifically address these complex issues.
Vitralit® UV 7030 is a one-component, solvent-free UV curable acrylic adhesive. It can be cured with light energy in the broad UV-A spectrum, or with LED systems that produce either 365 or 405 nm wavelength. This adhesive cures in seconds at layer thicknesses of a few 100 µm, ensuring high bond strength immediately after UV exposure. A key feature of Vitralit® UV 7030 is its high elongation at break, >250%, combined with good tensile strength. When exposed to black light, Vitralit® UV 7030 fluoresces, which enables visual process control. Vitralit® UV 7030 is certified to USP Class VI standards and suitable for typical sterilization processes including gamma, EtO and autoclave.
Download the technical datasheet: Vitralit® UV 7030
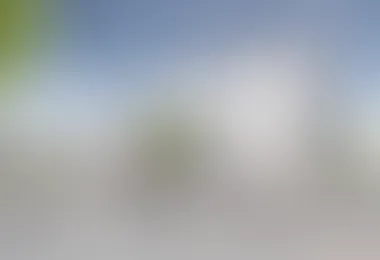
Tubes are bonded to connectors using Vitralit® UV 7030.
Steinbach/Germany, 9 July 2021
Panacol introduces new reworkable underfill adhesive
Panacol has developed a new reworkable underfill for consumer electronics. The reworkability and fluorescence despite its black color of the new Structalit® 5751 adhesive allows manufacturers to reduce both manufacturing costs and environmental impact by reusing electronic components mounted on PCBs.
Underfills serve the purpose of equalizing stresses between chip and substrate. Chips are attached directly to the interconnection points without intermediate elements. Stresses arise at the solder bumps when the electronic modules are heated and cooled during operation due to the different coefficients of thermal expansion of the substrates. Underfill technology was developed to counteract these mechanical influences.
Structalit® 5751 is a black, heat-curing, resin-based epoxy adhesive characterized by its low viscosity and linear flow behavior. These properties enable precise application. In addition to classic contact dispensing by means of a dispenser, the uncured properties of Structalit® 5751 also allow contactless dispensing for fast and precise placement of the adhesive. This underfill is has a low ion content and is ideally suited for electronic component packaging.
A typical feature of adhesives on PCBs is their black coloring, which is used to obscure proprietary features and for optical inspection. Optical measurement of an underfill is a common method used in the manufacturing process by manufacturers. But due to the dark chip, shallow layer thickness of the black adhesive and tight gap between the chip and the substrate, optical measurement is often difficult. Panacol has addressed this problem by incorporating an additional yellow shimmering fluorescence to the black coloration of Structalit® 5751. It can be stimulated by short wavelength light of <365nm. This makes it even easier for manufacturers to perform final inspections and speeds up production processes.
In addition to the performance and optical inspection capability of Structalit® 5751, Panacol offers another important property with its newly developed underfill: reworkability. This provides the ability to re-process or repair products after assembly. For manufacturers of electronic components, this challenge is becoming increasingly important as legislation and environmental associations push for the minimization of electronic waste. One starting point of this sustainable strategy is the reworkability and repairability of individual modules on printed circuit boards to counteract the scrapping of a complete component or module.
Structalit® 5751 can be strategically softened at specific adhesion points by applying temperatures above its glass transition temperature range of 150°C. The product becomes reworkable only when this critical temperature threshold is reached. The reworkability temperature does not reduce the protective function of the Structalit® 5751 during typical PCB processing. It withstands temperatures associated with reflow soldering and additional thermal curing cycles.
The current global shortage of chips and general electronic components in the automotive and consumer electronics sectors further highlights the significance of being able to reuse components. Reuse of components is not only a benefit to the environment, it has become essential to sustain current production processes due to supply chain shortages.
Download the technical datasheets:
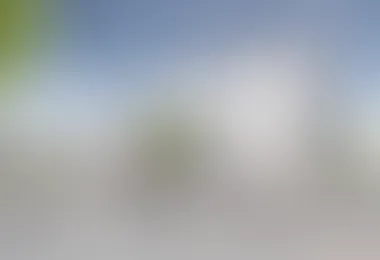
Underfill Structalit® 5751 seen under normal daylight and yellow fluorescing under uv light.
Steinbach/Germany, 9 June 2021
Panacol-Elosol relocates to newly constructed facility
Vigorous growth has enabled Panacol-Elosol GmbH, manufacturer of industrial and specialty adhesives, to build a larger facility for its corporate headquarters. With double the space for offices, laboratories and production, up to 100 employees can now work at the new site. It is located in Steinbach near Frankfurt/Main Germany, within the new Steinbach industrial estate "Im Gründchen", close to the company’s former location.
The new building offers Panacol employees a contemporary work environment with more than 6,000 m2 space. The laboratories for research & development, application engineering and quality management are equipped with state-of-the-art technology that increases in-house analytical and testing capabilities. A larger production area with additional new equipment has increased manufacturing capacity and efficiency. The new facilities can be expanded to support further growth in the coming years.
Panacol provides customer-focused assembly solutions based on innovative adhesive technology. This includes products for structural bonding, protective coating and encapsulation, electrical and thermal conduction, gasketing, and temporary masking. With subsidiaries in France, USA, China and Korea, Panacol provides global product supply and technical support.
Served markets include automotive, aerospace, optics, consumer and industrial electronics, luxury packaging, appliance, and medical device assembly. Customised adhesive solutions are developed and manufactured at the Panacol sites in Steinbach Germany and in the United States.
Panacol-Elosol GmbH was founded in 1978 as a German subsidiary of the Swiss Panacol AG in Frankfurt. In 2008, Panacol was acquired by Munich-based Dr. Hönle AG, a leading global supplier of industrial UV equipment technology. As a member of the Hönle Group, Panacol is a knowledgeable and reliable provider of adhesives, coatings, and UV/LED curing equipment for OEM and contract manufacturers around the world.
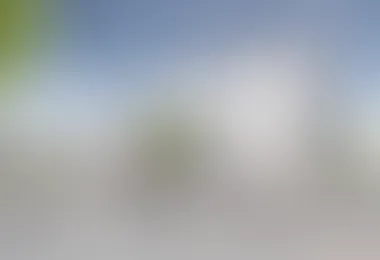
Aerial view of the new Panacol headquarter building in Steinbach near Frankfurt, Germany
Steinbach/Germany, 20 April 2021
New epoxy adhesives cure at 60°C
Panacol has developed a range of new one component epoxy adhesives that cure at very low temperatures. These new adhesives were developed specifically for electronics applications and adhere very well to substrates with low surface energy.
With the adhesives Structalit® 5511, 5521 and 5531, a range of adhesives has been developed that exhibit a unique set of physical properties after reaching full cure. This permits optimizing the adhesive with various component geometries, substrates, and operating functions.
All three adhesives are single-component, epoxy resin-based adhesives and cure at just 60°C, making them particularly suitable for temperature-sensitive electronic components. Curing at higher temperatures will accelerate cure time and add additional strength to the bond.
Structalit® 5511 features a particularly low ionic content and is therefore especially suitable for use in electronics. Combining a high Young's modulus with an elongation at break of more than 8%, it ensures high adhesion to many substrates with additional shock and vibration resistance.
Structalit® 5521 is softer and more flexible after curing, allowing the adhesive to better compensate for stresses between substrates. Due to its very low modulus of elasticity, this adhesive is very well suited for potting or for the application of thicker adhesive layers.
As the third adhesive of the new epoxy technology, Structalit® 5531 has an extraordinary low coefficient of thermal expansion (CTE), yet is flexible enough to withstand drop and vibration tests. The incorporation of filler particles gives the adhesive extremely high resistance to mechanical and chemical influences.
These Structalit® adhesives from Panacol generate very high bond strength with materials typically used in the electronics industry. They can also adhere very well to LCP (liquid crystal polymer) and other high-tech plastics with low surface energy. All three adhesives possess high purity and low ion content which complies with international standards for electronic and microelectronic component assembly.
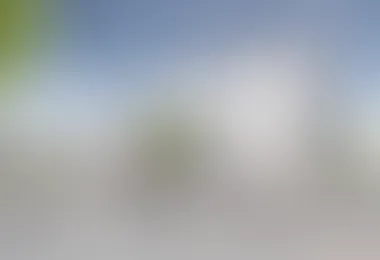
The new Structalit® 5511 is suitable for connector sealing (adhesive shown in light blue in the graphic).
Steinbach/Germany, 24 February 2021
Panacol introduces new high-performance frame-and-fill adhesives
Panacol has developed a new range of high-performance adhesives for frame-and-fill applications on printed circuit boards.
Frame-and-fill processes are used to protect highly complex areas on electronic circuit boards. In the first step, a highly viscous barrier – the so-called frame – is applied. In the next step, this area is quickly filled with lower viscosity filler material – the fill. With this precise process, areas on the circuit board can be protected from mechanical impact factors.The combination of frame-and-fill materials allows the application of minimum barrier and potting heights and cures to a homogeneous coating. Panacol's new frame-and-fill adhesives are perfectly matched so that the frame and fill areas can be optimally dispensed wet-on-wet without the still-liquid adhesives leading to undesired flowing on the PCB.
The frame material, Structalit® 5704, is a black, thermally curable and single-component epoxy. This frame and glob top compound features excellent bead stability and high glass transition temperature of 150°C up to 190°C, depending on the curing parameters and the layer thicknesses. When using Structalit® 5704, no bleeding effects occur. Due to the very low ion content of less than 20 ppm, Structalit® 5704 is suitable for chip encapsulation on electronic circuit boards.
As a fill material, Panacol has developed a range of adhesives with different rheological properties. The adhesives Structalit® 5717 to Structalit® 5721 are formulated with optimized flow behavior, so that the adhesives can be used on various chip and bonding wire geometries due to the differently adjusted viscosities. Since the fills have the same chemical base as the frame material, the excellent physical and chemical properties of high glass transition range, ion purity, temperature stability and minimal shrinkage behavior are also found in the fillls.
Once cured, Structalit® 5704 and the matching fill of the Structalit® 5717-5721 series form a black, opaque and scratch-resistant coating. These properties together with a temperature resistance of up to 200°C ensure maximum reliability.
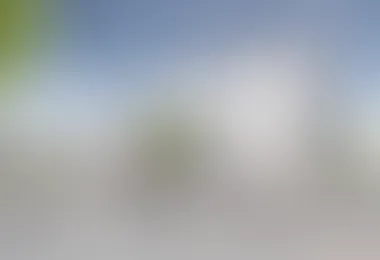
Structalit® 5704 is applied as a stable "frame" and then filled with low-viscosity fill material to form a homogeneous protective coating of sensitive components
Steinbach/Germany, 26 January 2021
Smart system solution for needle bonding
A main field of application for adhesives in medical systems is needle bonding and syringe assembly in high volume production. Optimally matched processes are essential for reliable bonding. Panacol, Hönle and bdtronic partner to ensure that precise adhesive dosing, capillary flow and curing in seconds with UV light work hand in hand.
As the needles are produced in large quantities rapid and reliable bonding is essential. In addition to their mechanical bond strength, the adhesives used must allow high-precision production and permanent joining and must withstand various sterilization methods. Panacol’s UV curable Vitralit® adhesives exactly meet these requirements. Vitralit® adhesives are available in various viscosity ranges to perfectly fit the design of the needle hub and fill the gap between the hub and the needle. The material of the hub and needle also affects the choice of the adhesive: Many adhesives are UV-curing, which requires the use of transparent and UV-permeable materials. For materials that block UV light, such as polycarbonates, long-wave LED curable adhesives are recommended.
All Vitralit® adhesives recommended for needle bonding are solvent-free and certified USP Class VI and/or ISO 10993 for use in medical equipment. In addition, high needle extraction forces were measured with all needle bonding adhesives even after several sterilization cycles. For visual quality inspection, fluorescent versions of our medical grade adhesives are also available.
The choice of the adhesives requires a matching dispensing system for reliable and precise dispensing in a rapid production environment.
The high quality demands required for medical devices, as this needle bonding application, confirms the choice for bdtronic’s volumetric dispensing equipment. With the mini-dis solution provided by bdtronic, dispensing in microliter range is made easy, regardless of the adhesive viscosity. Thanks to the continuous volumetric dispensing, the dispensing is pulsation free ensuring optimal process speed, repeatability and accuracy.
Finally, the choice of the UV curing equipment depends on the adhesive and the wavelength which triggers polymerization. For needle bonding with Vitralit® products you can use either UV-A or visible LED light.
Due to a special LED assembly and an own optimized electric power supply, Hönle LED Powerline LC guarantees a high-intensive irradiation for fastest curing and shortest cycle times. In addition, the irradiation time can be selected in a range of 0.01 – 99.99 sec and thus precisely adapted to the process requirements.
Hönle LED Powerline heads have a compact design for an easy integration into any production line. The high-intensive, water-cooled LED-UV is suitable for clean room operation.
More information on dispensing equipment from bdtronic and uv light curing systems from Dr. Hoenle
Read more about our Needle Bonding solutions
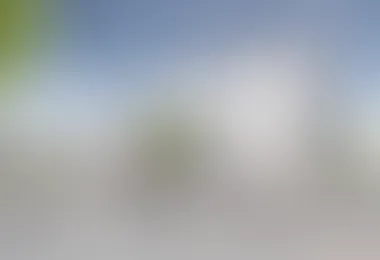
The UV adhesive bonding the needles into the needle hubs is being cured under uv light.
Watch "Needle Bonding" video:
Steinbach/Taunus, 20 november 2020
New dual-curing potting compound for piezoceramics
Panacol is expanding its portfolio of dual-curing acrylic adhesives with the introduction of Vitralit® UD 8052 F. This material was developed for piezo actuators and sensors. It possesses a particularly high tear resistance for bonding ceramics and plastics.
Vitralit® UD 8052 F is a low viscosity, one-component UV curable adhesive. It is jettable, transparent, and fluoresces under UV light. Customized versions with different colors are available to facilitate improved process control. Its jet dispense capability makes high UPH (units per hour) values achievable, which is why Vitralit® UD 8052 F is the perfect choice for consumer electronics applications.
This potting compound can be cured in just a few seconds with UV light (320nm - 390nm) or visible light (405nm). The fluorescing adhesive allows in-line process control with short-wave light for maximum productivity. In areas that cannot be reached by light, Vitralit® UD 8052 F post cures with atmospheric moisture, and thus polymerizes reliably into a flexible potting and glob top compound.
Its high tear resistance after curing has been optimized for bonding ceramic components to plastic, compensating for the different expansion coefficients of the bonded materials. Thus Vitralit® UD 8052 F is particularly suitable as a protective coating and for applications subject to tensile and compressive stresses. As a potting compound, it features a low halogen content, it is flexible and offers protection against corrosion and other environmental influences.
Download technical datasheet for Vitralit® UD 8052 F
Read more about adhesive application in electronics
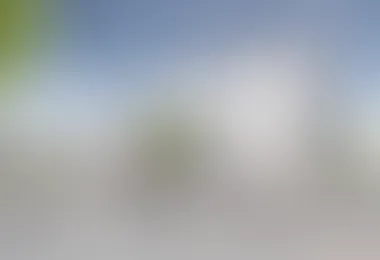
Fluorescence testing of a strand protected with Vitralit® UD 8052 F on a piezo actuator.
Steinbach/Germany, 1 October 2020
Panacol and Hönle develop new system solution for filament winding processes
With the newly developed Vitralit® UD 1405 adhesive, Panacol has created an innovative adhesive system for fibre and filament winding. For high efficiency, Vitralit® UD 1405 can be applied during the winding process and immediately cured with high intensity LED curing systems from Dr. Hönle AG. This innovative winding process is extremely space and time-saving, and can produce significant processing cost savings.
Vitralit® UD 1405 can be used to wrap components such as hybrid rotor shafts for electric motors and high-voltage surge arresters. The adhesive-coated fibre-reinforced windings can be then be quickly cured with UV/visible light. This adhesive and curing system is ideal for Carbon or Glass Fibre filament winding associated with Carbon Fibre Reinforced Polymer (CFRP) or Glass Fibre Reinforced Polymer (GFRP) manufacturing processes.
Panacol’s Vitralit® UD 1405 is a transparent, solvent-free, one-component epoxy. Due to its low viscosity, Vitralit® UD 1405 has very good wetting properties. It can be cured in seconds by irradiation with UV (365nm) or Visible (405nm) light wavelengths. Depending on the fibre material and the wavelength used, layer thicknesses of several millimetres can be achieved exclusively by UV/Visible light curing. This epoxy can also be thermally cured after UV exposure to ensure that a complete cure is secured in areas shadowed from the UV light. For example, fibres or filaments can first be pulled through an adhesive bath, then wound onto the rotor or respective cylinder, and cured with UV or visible light. A secondary thermal cure will ensure that the layers of coated windings below the surface become fully cured.
For the most efficient UV curing system for fibre and filament winding processes, the LED Powerline AC/IC 820 HP from UV specialist Hönle is the perfect choice. With intensities of up to 16,000 mW/cm², this LED system ensures very fast curing. Its light emission window is available in two standard sizes, 82 mm x 20 mm and 122 mm x 20 mm, which can be extended without gaps by stringing together multiple modules. When developing the LED Powerline AC/IC 820 HP, special attention was paid to a slim design. This makes it ideal for use where space is at a premium, such as automated winding equipment.
The powerful LED Powerline AC/IC 820 HP can be powered and controlled using the optionally available LED powerdrive IC as a plug&play solution, or by using a customer supplied external power supply and PLC. This makes the LED Powerline an ideal solution for integrating high power LED curing systems into automated assembly processes.
After curing, Vitralit® UD 1405 is electrically insulating, shows minimal shrinkage and remains resistant at temperatures from -40° to 180°C. A glass transition temperature of over 130°C ensures reliable performance even under dynamic load at elevated temperatures.
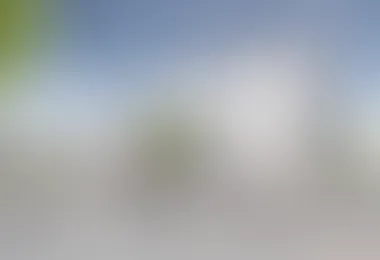
The winding of a filament impregnated with Vitralit® UD 1405 is cured under UV LED light
Steinbach/Taunus, 28 August 2020
New UV Adhesive for Decorations and Dome Coatings
Vitralit® UC 6685 was formulated by Panacol specifically for decorations on plastic, glass or metal. Due to its slight magnifying property, the transparent adhesive produces a high-quality image of the structures and illustrations underneath.
Vitralit® UC 6685 is a transparent, UV-curing adhesive based on epoxy resin. Being one-component the adhesive is easy to dispense. Its viscosity makes it suitable for decorative applications on flacons and bottles or for dome coatings, an elegant protective coating for key rings, lapel pins, buttons, name tags, pens and jewelry, for example.
Under UV light in the wavelength range from 320 nm to 390 nm, Vitralit® UC 6685 can be cured in just a few seconds, enabling a high cycle rate in the production process. The in-house UV and LED UV systems of Dr. Hönle are perfectly matched to the adhesive for particularly fast and easy curing under UV light.
After curing, Vitralit® UC 6685 is very hard and scratch-resistant, it is characterized by its brilliant transparency and does not yellow as it ages.
Download TDS Vitralit® UC 6685
More information about our adhesive solutions for luxury packaging
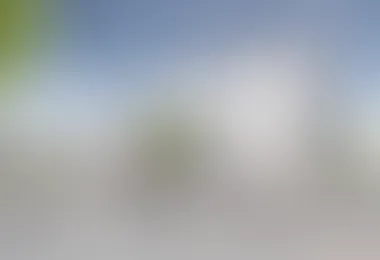
Adhesive drops for decoration on a glass flacon
Steinbach/Taunus, 16 June 2020
Adhesives for Cell Contacting Systems and Battery Packs
Panacol has developed specially formulated UV adhesives that protect welded joints on cell contacting systems and battery packs of electric cars from corrosion. The flexible adhesives enable vibration-resistant connections and have a low ion content.
High-performance cell contacting systems (CCS), which combine individual lithium-ion battery cells for hybrid and electric vehicles to form battery packs, are often connected by welded strands or wires. To protect these welded joints from corrosion, Panacol has developed special low-ion UV adhesives that are applied as protective coatings. These adhesives provide additional mechanical support when subjected to vibrations and can compensate for thermal expansion of the different materials.
UV-curing adhesives Vitralit® UV 2113 and Vitralit® UV 2114 are characterized by very high adhesion to many materials and meet the requirements of the automotive industry in terms of media and temperature resistance. The rheological properties of both Vitralit® UV 2113 and Vitralit® UV 2114 can be adapted to individual customer requirements. Fluorescent adhesive variations for optical process control are also available.
In just a few seconds, these adhesives can be cured with light in the UVA or visible range. Both gas discharge lamps and LED spot systems can be used for curing. Perfectly matched to Panacol adhesives are the UV and LED UV curing systems from Dr. Hönle, for example the high-intensity LED Powerline AC/IC HP.
For complex CCS geometries with shadowed areas, dual curing Vitralit® UD 8050 is the perfect choice. After UV irradiation, this ion-pure acrylate adhesive post-cures in the shadowed areas by reacting with humidity in the air.
Download technical datasheets of Vitralit® UV 2113, Vitralit® UV 2114 and Vitralit® UD 8050
More information on bonding applications for battery packs and cell contacting systems
Biocompatible Adhesive Withstands High Heat Input
The epoxy resin based Vitralit® 1605 is particularly unique due to its high glass transition temperature and is therefore versatile for applications with high heat input. The biocompatible adhesive cures under UV light and is suitable for medical device assembly.
The one-component adhesive Vitralit® 1605 from Panacol is transparent and very easy to dispense. Its adhesion to glass and metal is excellent, which is why it can be used for fixing glass and rod lenses in endoscopes or for bonding lens stacks, for example.
The cationic Vitralit® 1605 can be cured under UV light in the wavelength range from 320 nm to 390 nm. It also features a thermal initiator that enables secondary curing of shadowed areas. The UV lamps from Dr. Hönle AG are well-matched for this adhesive, delivering fast and consistent curing processes.
When fully cured, Vitralit® 1605 is characterized by excellent chemical resistance and very low shrinkage. In addition, it has a very high glass transition temperature of 150°C and a low coefficient of thermal expansion. This provides the ability to bond components that require maximum stability during elevated operating temperatures. Furthermore Vitralit® 1605 can withstand the typical sterilization processes. Due to these characteristics, as well as its certification according ISO 10993-5, Vitralit® 1605 is especially suitable for bonding in medical technology.
Download technical data sheet
Blue markings show the exemplary application of the Vitralit® 1605 adhesive for bonding rod lenses in endoscopes.
(Click to enlarge)
Steinbach/Taunus, 18 March 2020
New Thermally Conductive Adhesive for Heat Sensitive Components
The new Elecolit® 6607 adhesive from Panacol is thermally conductive and can be oven cured at temperatures as low as 80°C. It is characterised by excellent metal adhesion and is electrically insulating.
Elecolit® 6607 is an epoxy resin-based adhesive filled with aluminium oxide. It is a one-component adhesive and due to its flow characteristics, it can be applied by dispenser, screen printing or spatula.
Since Elecolit® 6607 cures at temperatures as low as 80°C, even heat-sensitive components can be bonded together. Curing at higher temperatures will shorten the curing time.
After curing, the light gray adhesive insulates electrically and provides excellent heat dissipation. Due to its properties, Elecolit® 6607 is particularly suitable for bonding metal components and heat sinks to electronic circuit boards.
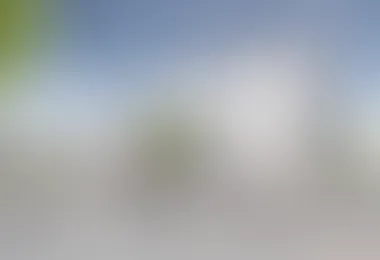
New adhesive Elecolit® 6607 is thermally conductive and can be cured from temperatures of 80°C.
Steinbach/Taunus, 13 February 2020
New Autoclavable UV Coating
Vitralit® 2028 from Panacol is a new UV curable coating that is resistant to chemicals and is autoclavable. It is a flexible coating material that can be cured in two ways, UV or heat.
The transparent epoxy Vitralit® 2028 is easy to dispense because of its low viscosity. Nevertheless, it enables a clean edge finish without bleeding. It is therefore ideally suited as a flexible protective coating.
Vitralit® 2028 can be cured with light energy in the UV range from 320nm to 390nm. UV curing devices from the UV equipment manufacturer Dr. Hoenle are particularly suitable for an optimal UV curing process. The special feature of the adhesive is its thermal initiator, which allows secondary curing of shadowed areas using an oven.
The coating surface is very dry after UV curing, so coated components can be processed immediately. The final strength of the UV coating is achieved when the it cools down to ambient temperature. Once fully cured, Vitralit® 2028 is transparent and resistant to chemicals and is suitable for autoclaving. This material is ideal as a protective coating for wires in coil windings as well as other applications requiring protective coatings.
Download technical data sheet
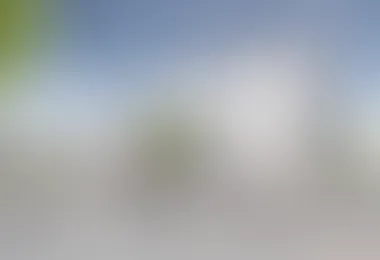
Vitralit® 2028 is used as the coating of a coil winding to protect against chemicals.
Steinbach/Taunus, 20 January 2020
New UV Adhesive with Low Halogen Content
With Vitralit® UC 1536 Panacol is launching another low-halogen UV adhesive for the electronics industry. Due to its low ion-content, it is ideal for semiconductor production. The new very stable, high-gloss, transparent adhesive cures within a few seconds.
The adhesive Vitralit® UC 1536 is an epoxy-based adhesive, which hardens very quickly under UV-light. Due to its high viscosity, it is particularly suitable for applications that require dimensional stability within the production process.
When exposed to light energy in the UVA range from 320 to 390 nm, the Vitralit® UC 1536 adhesive can be cured within seconds. Panacol offers a broad line of suitable curing devices from Dr. Hönle that can create customized solutions for the processing of Vitralit® UC 1536. UV bonding and curing solutions are available for every application from a single source!
Vitralit® UC 1536 cures to an optically clear and high-gloss surface, which is very hard and scratch-resistant. Even at high operating temperature, the adhesive remains very clear and keeps its transparent brilliance. Characterized with a very low ion-content, Vitralit® UC 1536 is ideally suitable for semiconductors. A very successful application for this adhesive involves bonding glass lenses to CMOS sensors.
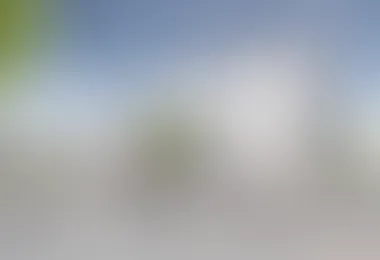
Individual parts of camera modules are fixed with adhesive such as Vitralit® UC 1536
Steinbach/Taunus, 15 November 2019
Fast Curing Epoxy Adhesive Enables High Efficiency Cosmetic Packaging
The new epoxy-based adhesive Vitralit® UC 6025 from Panacol optimizes automated assembly processes. It can be applied and cured very quickly due to its accommodating dispensing properties.
Especially designed for the cosmetics industry, Vitralit® UC 6025 has an optimal viscosity for gap-filling applications. The one-component epoxy adhesive is odourless and easy to dispense. Its controllability and fast curing properties make Vitralit® UC 6025 suitable for applications requiring a high performance.
Vitralit® UC 6025 can be cured with UV or visible light in just a few seconds. The adhesive curing process can be further optimized by using UV/LED curing equipment from Dr. Hönle. The fluorescing version of the adhesive, Vitralit® UC 6025 F, allows in-line process control for maximum productivity.
Once cured, the adhesive has high adhesion to ABS, aluminium and glass. These properties and lack of odour make Vitralit® UC 6025 ideal for applications in the cosmetics industry. Application examples include bonding lipstick applicators or bottle lids.
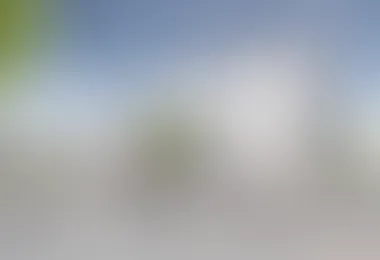
New epoxy adhesive Vitralit® UC 6025 is the perfect bonding solution for high volume production of plastic packagings
New Biocompatible Adhesive for Plastics Fluoresces Orange
A new orange fluorescent UV adhesive from Panacol is specially formulated for bonding plastics: Vitralit® 7311 FO is certified according to USP Class VI standards which makes it the perfect solution for bonding medical devices.
Vitralit® 7311 FO is a low viscosity, transparent acrylic adhesive that cures under UV or visible light. It offers very high bond strength to many plastics including PC, PVC, PMMA or ABS, and also to materials such as glass and stainless steel. Thanks to its very low viscosity and capillary flow characteristics, Vitralit® 7311 FO is suited for bonding large surfaces as well as applications with narrow gaps.
Under low intensity black light (365 nm wavelength), Vitralit® 7311 FO fluoresces orange. This allows in-line inspection for quality control. The bright fluorescence is highly contrasting with plastics possessing a natural blue fluorescence or color. Optimum curing results can be achieved with LED curing equipment with a wavelength of 405 nm, especially the UV-LED equipment Bluepoint LED eco from Hoenle. Bluepoint LED eco can be equipped with both wavelengths, serving both processes. Thanks to modern photo initiators Vitralit® 7311 FO can be cured – especially in high volume production – within seconds.
Once cured, Vitralit® 7311 FO is humidity and alcohol resistant. Vitralit® 7311 FO has been tested and certified according to USP Class VI standards. The product is compatible to common sterilization processes like autoclaving, gamma radiation, E-Beam or ETO and well suited for use in the assembly of disposable medical devices.
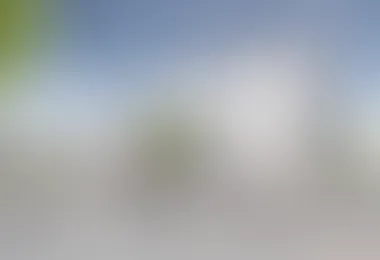
Vitralit® 7311 FO fluoreces orange.
Steinbach/Taunus, 26 August 2019
New Crystal-Clear UV Adhesive for Semiconductor Production
At this year’s BondExpo Panacol will present Vitralit® UC 1535, a new transparent adhesive specifically designed for use in electronics. It hardens with UV light within a few seconds and can be used for semiconductor production due to its low ion content.
The Vitralit® UC 1535 is an epoxy-based UV-curing adhesive that hardens very fast. It is easy to dispense and non shear-thinning. In just a few seconds, the adhesive can be cured with radiation in the UVA range from 320 to 390 nm. For a fast and efficient curing, the broad spectrum and UV/LED systems from Dr. Hoenle AG are highly recommended.
The adhesive was especially designed for the assembly and production of electronic and optomechanical components. For example, the new Vitralit® UC 1535 is being used to bond glass lenses in optical systems. Once cured the adhesive features a transparent, optically clear and brilliant surface, which is very hard and scratch-resistant. Vitralit® UC 1535 is non-yellowing and remains optically clear even when exposed to high temperatures. Because of its low ion content the adhesive can be used for semiconductor applications.
Visit us at the BondExpo in Stuttgart, Germany from the 7th to the 10th of October 2019 at booth 6420 in hall 6!
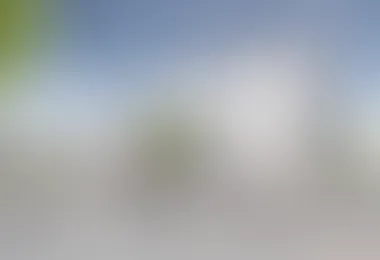
Vitalit® UC 1535 from Panacol is designed for the assembly and production of electronic and optomechanical components.
Eleco Produits – EFD to become Eleco Panacol – EFD
French company Eleco Produits – EFD, specialising in industrial adhesives, dispensing and uv curing equipment, and German based adhesives manufacturer Panacol-Elosol GmbH, are both members of the adhesives division within the Hoenle Group, headed by publicly listed company Dr. Hoenle AG. To better support the growth requirements of their global customers, and present a more unified product offering, Eleco Produits – EFD is changing its name to Eleco Panacol – EFD effective August 1, 2019. “With this decision we see synergies in marketing and global brand recognition for the Panacol Group”, explains Laurent Prevost, Managing Director of Eleco Panacol – EFD.
Eleco Produits – EFD has been specializing in the distribution of industrial adhe-sives and matching dispensing and curing equipment since 1974. Since the beginning, Eleco has been partnering with German adhesives manufacturer Panacol-Elosol, distributing uv, structural and conductive adhesives. Inhouse laboratories for quality control and adhesive applications allow in-depth testing and qualified consultation. Since 2008, Eleco has also been distributing matching uv curing equipment from new parent company Dr. Hoenle. To complement its all-in-one solutions, Eleco also provides dispensing equipment for its adhesives portfolio. Situated in the metropolitan Paris area, Eleco benefits from a central logistic hub. Effective quality control methods ensure high quality products, packaging and transport. Eleco is certified to ISO 9001 standards.
The focus of Eleco Panacol – EFD will remain on the sales of innovate industrial adhesives and equipment from its facility in Genevilliers/Paris. The organization’s management and team will remain intact.
Visit Eleco-Panacol website
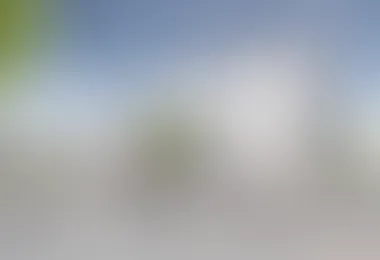
Eleco Panacol - EFD in Paris area, France
New Optically Clear Adhesive
Panacol developed a new optically clear adhesive: Vitralit® 50004. The new adhesive is a one-component uv curable acrylic adhesive with ultra-low viscosity, which is used for bonding displays and laminating optics.
Vitralit® 50004 adheres specifically to a variety of substrates including coated glass, PET and other plastics and films. It possesses a very low viscosity that facilitates fast filling of cavities without air entrapment. The adhesives cures quickly with minimal shrinkage for less residual stress between substrates.
Large-surface bonding or lamination of displays can be optimized by using Hoenle’s high-performance and energy efficient LED Spot 100 curing system which is perfectly matched to the photoinitiators of Vitralit® 50004.The alignment of the LEDs of the Spot 100 ensures high intensity and homogeneous light distribution. The LED Spot 100 heads can be mounted together without gaps to match the size of the display being bonded.
Once cured, Vitralit® 50004 is very soft. Thermal stresses between dissimilar substrates can be neutralized without causing delamination. It’s high degree of flexibility enhances performance through repeated thermal excursions. The cured adhesive is optically clear and non-yellowing with excellent light transmission.
Download technical data sheet
Read more about our LOCA adhesives
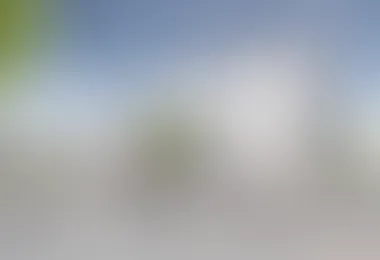
LOCA adhesives from Panacol are the perfect solution for serial production of displays and touchscreens
New Panacol Adhesives Cure With UV/moisture
Panacol developed a variety of new adhesive products with low ion content which cure with uv light and moisture. These products were specially formulated for applications in the electronics and consumer electronics industry, where heat sensitive parts must be assembled.
Vitralit® UD 8050 is a one-component acrylic adhesive, which can be used as an encapsulant to protect electronic components on PCBs. Vitralit® UD 8050 can be cured with uv or visible light. Moisture postcuring ensures full cure in shadowed areas or deeper layers of the adhesive, which cannot be reached by light.
For specific requirements several versions of the adhesive are available: Vitralit® UD 8050 MV F allows enhanced flow control and focused dispensing on each component thanks to its shear-thinning behavior. Its low ion content prevents cor-rosion on electronic components. For superior process control Vitralit® UD 8050 MV F contains a fluorescent marker.
For jetting, the low viscosity version Vitralit® UD 8050 LV is the perfect solution. Thanks to its easy dispensing and fast curing Vitralit® UD 8050 LV is very conven-ient for applications in the production of consumer electronics where a high throughput is needed.
By default, the adhesive is transparent, but it is also available in blue or fluorescing versions. Other colors are available on request.
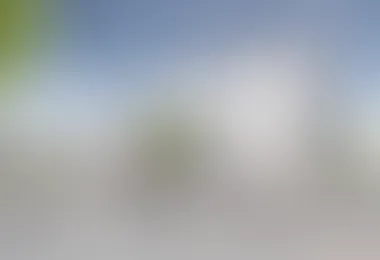
Blue uv-moisture curing adhesive is used as encapsulant for electronic components
Tangent Industries Inc. to become Panacol-USA Inc.
US adhesives and coatings manufacturer Tangent Industries Inc., based in Torrington, Connecticut and German based adhesives manufacturer Panacol-Elosol GmbH, are both part of the adhesives division within the Honle Group. The head of the Honle Group is the publicly listed company Dr. Hoenle AG. To better support the growth requirements of their global customers, and present a more unified product offering, Tangent Industries Inc. is changing its name to Panacol-USA Inc. effective October 1st, 2018. Moreover, Panacol-Elosol will gradually assume full ownership of the new Panacol-USA within a 5 year span. “With this decision we see synergies such as global marketing and to provide adhesive products under one brand to our worldwide acting customers”, explains Florian Eulenhöfer, Managing Director of Panacol-Elosol GmbH.
Tangent Industries Inc. has been specializing in the development and production of UV curing acrylic adhesives and coatings since 1994. Panacol was the distributor for Tangent products outside the Americas since the very first day. The focus of Panacol-USA Inc. will remain on the development, production, and sales of innovate UV acrylic adhesives and coatings from its facility in Torrington. The organization’s management and team will remain intact.
Panacol-Elosol GmbH and Panacol-USA Inc., both members of the global Hoenle group, are leading suppliers of industrial adhesives, with a broad product range that includes UV curable adhesives and coatings, structural epoxies and conductive materials for electronics assembly. Panacol-USA Inc. is also a reliable provider of UV/LED processing systems in the Americas, designed and manufactured by Dr. Hoenle AG, a global technology leader of industrial UV curing devices and systems.
Visit website panacol-usa.com
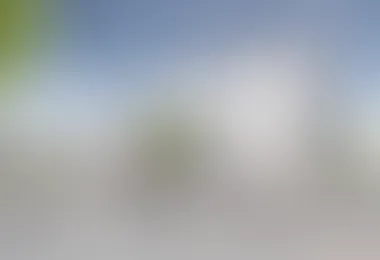
Panacol-USA Inc. in Torrington, Connecticut