Encapsulation of Electronic Components
Epoxy and acrylate resin based sealing and potting compounds are often used in electronics to protect electronic components, semiconductors and subassemblies. The encapsulation protects components from moisture, dust, dirt and solvents. Used to fill cavities or encapsulate components, sealing compounds also provide effective protection from mechanical stress.
All Panacol sealing or potting compounds are made without solvent and many have a low ionic content of less than 10 ppm Na+, K+, Cl- and Br-. They therefore provide perfect protection from internal corrosion and reduce local voltaic coupling.
Many sealing compounds are UV-curing, allowing rapid setting in just a few seconds. This makes them suitable for encapsulating components in fully automated high-volume production.
Thermally curing potting compounds, on the other hand, have the advantage of curing even in dark areas that the UV light cannot reach. These encapsulants are also available in black colour for use as a coating or covering.
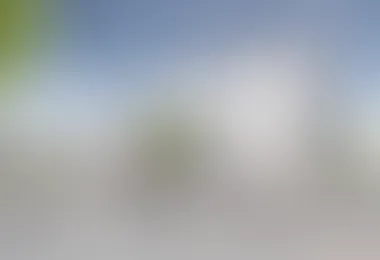
A black sealing compound is used to protect mass-produced chips
The table below lists a selection of encapsulants, sealing and potting compounds from Panacol. Further products and custom solutions are available on request.
To download the technical datasheets (TDS) please click on the adhesive name.
Potting Compound | Viscosity [mPas] | Base | Curing* | Properties |
---|---|---|---|---|
Structalit® 5511 | 800-1,200 | epoxy | thermal at 60°C |
Non-conductive Outstanding adhesion to high performance plastics (LCP, PBT) High purity Electronic grade standard |
Structalit® 5521 | 1,200-2,000 (Rheometer, 25°C, 10s^-1) | epoxy | thermal at 60°C |
Non-conductive Outstanding adhesion to high performance plastics (LCP, PBT) High purity Electronic grade standard Flexible |
Structalit® 5531 | 5,000-10,000 (Rheometer, 25°C, 10s^-1) | epoxy | thermal at 60°C |
Non-conductive Outstanding adhesion to high performance plastics (LCP, PBT) High purity Electronic grade standard Good mechanical stability Good chemical resistance |
Structalit® 5800 | 7,000-15,000 mix (LVT, 25°C, Sp. 4/30 rpm) | 2-part epoxy | thermal, room temperature |
High temperature resistance short pot life fast application |
Structalit® 5801 | 12,000-22,000 mix, 10,000-20,000 part A, 18,000-29,000 part B, (Rheometer, 25 °C, 10s^-1) | 2-part epoxy | thermal, room temperature |
Black color Excellent oil, chemical and moisture resistance Low shrinkage Low water absorption Good adhesion to metal, glass and plastics |
Structalit® 5802 | 40,000-65,000 mix (Rheometer, 25°C, 10s^-1) | 2-part epoxy | thermal, room temperature |
Dark grey color Excellent oil, chemical and moisture resistance Low shrinkage Low water absorption Good adhesion to metal, glass and plastics Flame classification based on UL 94 HB |
Structalit® 5810-1 | 3,000-4,000 mix (LVT, 25°C, Sp. 4/30 rpm) | 2-part epoxy |
thermal room temperature |
Very high adhesion to PC resistant to moisture and chemicals |
Structalit® 5891 | 25,000-50,000 ( Rheometer, 25 °C, 10s-1 ) | epoxy | thermal |
Black color fast curing at low temperatures impact resistant |
Structalit® 5891 T | 80,000-150,000 (Rheometer, 25 °C, 10s^-1 ) | epoxy | thermal |
Black color stable frame material, can be applied wet-in-wet with filling material, suitable for frame stacking stable edges resistant to shocks |
Structalit® 5893 | 6,000-10,000 (Rheometer, 25°C, 10s^-1) | epoxy | thermal |
Black color excellent flow properties filling material for frame&fill applications high resistance to heat and chemicals certified to ISO 10993-5 standards |
Structalit® 5894 M | 20,000-30,000 (Rheometer, 25 °C, 20s ^-1) | epoxy | thermal |
Black color excellent flow properties filling material for frame and fill applications on PCBs, very high resistance to heat and chemicals |
Structalit® 8801 | 30,000-45,000 (LVT, 25°C, Sp. 4/6 rpm) | epoxy | thermal |
Resistant to oils, grease and fuels excellent flow properties beige color certified to ISO 10993-5 standards |
Structalit® 8801 black | 30,000-45,000 | epoxy | thermal |
Resistant to oils, grease and fuels black color excellent flow properties |
Structalit® 8801 T | 16,000-30,000 (Rheometer, 25 °C, 5s^-1) | epoxy | thermal |
Resistant to oils, grease and fuels; Stable; Fast curing at low temperatures |
Structalit® 8805 | 30,000-45,000 | epoxy | thermal |
Resistant to oils, grease and fuels excellent flow properties beige color |
Structalit® 8838 | 6,500-7,500 (Rheometer, 25°C, 20s^-1) | epoxy | thermal |
Black color flexible potting compound excellent flow properties |
Vitralit® 1600 LV | 3,000-5,000 | epoxy |
UV secondary heat cure |
Very high Tg low water absorption low ion content very high chemical resistance |
Vitralit® 1605 | 200-400 (LVT, 25°C, Sp. 2/30 rpm) | epoxy |
UV secondary heat cure |
low shrinkage low heat expansion very high tg excellent chemical resistance certified to ISO 10993-5 standards |
Vitralit® 1650 | 3,000-5,000 | epoxy | UV |
Electronic grade low ion content suitable for chip protection UL94 HB test passed |
Vitralit® 1655 | 150-300 (Brookfield LVT, 25 °C, Sp. 2/30 rpm) | epoxy |
UV secondary heat cure |
flexible certified to USP Class VI and ISO 10993-5 standards resistant to all common sterilization methods |
Vitralit® 1657 | 5,000-15,000 | epoxy | UV |
Low ion content excellent chemical resistance low water absorption suitable for covering open bonded chips |
Vitralit® 1671 | 9,000-14,000 (Rheometer, 10s^-1) | epoxy |
UV secondary heat cure |
Stable frame compound high ion purity electronic grade adhesive high temperature conductivity low water absorption UL94 HB test passed |
Vitralit® 1680 | 5,000-8,000 | epoxy | UV |
Very high resistance to heat and humidity electronic grade adhesive low ion content suitable for chip protection |
Vitralit® 1688 | 1,200-2,000 | epoxy | UV |
Excellent flow properties and leveling electronic grade adhesive low ion content suitable for chip protection excellent resistance to heat and humidity |
Vitralit® 1691 | 20,000-40,000 | epoxy |
UV secondary heat cure |
black color high ion purity electronic grade adhesive high temperature resistance fast surface curing with UV light |
Vitralit® 1720 | 2,700-3,700 (LVT, 25 °C, Sp. 2/6 rpm) | epoxy | UV | High temperature resistance |
Vitralit® 1722 | 5,000-8,000 (LVT, 25 °C, Sp. 4/30 rpm) | epoxy | UV |
Very high adhesion to most thermoplastics low shrinkage high temperature resistance |
Vitralit® 2004 F | 60-100 (LVT, 25 °C, Sp. 2/30 rpm) | epoxy |
UV secondary heat cure |
fluorescing flexible autoclavable dry surface after curing low ion content sprayable |
Vitralit® 2007 F | 150-350 (LVT, 25 °C, Sp. 2/30 rpm) | epoxy |
UV secondary heat cure |
fluorescing flexible autoclavable excellent chemical resistance low ion content |
Vitralit® 2028 | 160-300 | epoxy |
UV secondary heat cure |
Dry surface after UV-curing autoclavable excellent chemical resistance scratch resistant coating |
Vitralit® 2009 F | 100-200 | epoxy |
UV secondary heat cure |
fluorescing flexible autoclavable high chemical resistance low ion content |
Vitralit® 4451 MV F | 2,000-3,000 (LVT, 25 °C, Sp. 4/30 rpm) | acrylate | UV, VIS |
soft and elastic dry surface after curing protective coating fast curing fluorescing blue |
Vitralit® 5140 | 250-500 | acrylate |
UV VIS |
Flexible, well suited for bonding plastics with low UV translucence and permeable to visible light, biocompatible: certified to USP Class VI standards |
Vitralit® 6103 | 3,500-5,000 | acrylate |
UV secondary heat cure |
Very high adhesion to metals and sintered materials transparent |
Vitralit® 6104 | 3,000-8,000 | acrylate |
UV secondary heat cure |
Very high adhesion to metals and sintered materials |
Vitralit® 6104 VT | 8,000-17,000 (Rheometer, 25°C, 10s^-1) | acrylate |
UV secondary heat cure |
Very high adhesion to metals and sintered materials ideal for bonding large components on circuit boards (corner bonding) |
Vitralit® 6105 | 3,500-6,000 | acrylate |
UV secondary heat cure |
very high adhesion to metals and sintered materials |
Vitralit® 6125 | 4,000-6,000 (LVT 25°C, Sp. 4/30 rpm) | acrylate |
UV secondary heat cure |
excellent adhesion to stone, glass, metals and thermoplastics medium viscosity |
Vitralit® 6128 | 800-1,200 | acrylate |
UV secondary heat cure |
very high adhesion to stone, glass, metals and thermoplastics high temperature resistance |
Vitralit® 6128 VT | 3,000-6,000 (Rheometer, 25°C, 10s^-1) | acrylate |
UV secondary heat cure |
contains chemical activator high temperature resistance high viscosity excellent adhesion to stone, glass, metals and thermoplastics |
Vitralit® 9179 | 200-400 | acrylate | UV |
Fast curing very well suited for automated production lines yellow color dry surface |
Vitralit® 9180 | 700-1,200 | acrylate | UV |
Dry surface fast curing of thick layers yellow color |
Vitralit® 9181 | 4,000-7,000 | acrylate | UV |
Yellow color dry surface fast curing of thick layers |
Vitralit® UD 5180 | 4,000-6,000 | epoxy |
UV secondary heat cure |
Perfect solution for bonding flexible circuit paths resistant to reflow processes grey color |
Vitralit® VBB-1 | 1,000-1,500 | acrylate |
UV VIS |
Elastic high peel strength optically clear very flexible suitable for potting |
Vitralit® UD 8055 | 5,000-8,000 (Rheometer, 25°C, 10s^-1) | acrylate |
UV VIS moisture cure |
High Tg Fast curing Compatible with flux Low ion content |
Vitralit® UD 8056 | 3,000-6,000 (Rheometer, 25°C, 10s^-1) | acrylate | UV / VIS / Moisture postcuring |
High Tg, fast curing Compatible with flux Low ion content Passed UL94 HB test |
*UV = 320 - 390 nm VIS = 405 nm