Bonding Solutions for Mini Camera Systems
Modern vehicles have a large number of miniature cameras: Rear view cameras help when parking and reversing, driver assistance systems support when changing lanes or other driving situations, other cameras help with traffic sign recognition, to name just a few examples. These mini cameras are embedded in the body and are so small that they cannot be bolted into place: Instead, special adhesives adapted to the respective materials are used to bond the plastic housings and fix the lenses. Panacol offers a range of product solutions for this.
Active Alignment
Active Alignment involves fitting lenses into the camera body and adjusting the focus. As soon as the position of the lens is exactly right, the adhesive is cured in a fraction of a second using UV light. The demands on the adhesive are high to achieve high-precision bonding: Not only must the adhesives cure very quickly, they must also have low water absorption and low and reproducible shrinkage to avoid tension.
Bonding of Housings
Camera housings consist of many individual parts that must be glued together. For this purpose, adhesives are used which have a high adhesion to the substrates to be bonded and which also seal the camera against dirt, dust and moisture.
Lens Bonding
In complex camera systems several lenses are used. In order to fix these lenses in a space-saving way, they are glued to each other. The adhesive must not only be extremely transparent and non-yellowing, but also scratch-resistant and resistant to moisture.
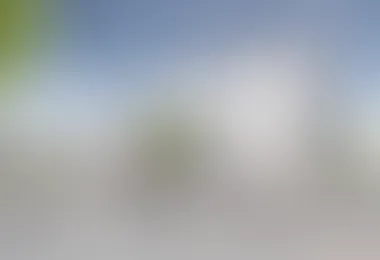
Only with adhesives can the small camera systems be securely joined
Download:
In the following table you will find a selection of adhesives used for the different applications in camera systems. Further products and customized solutions are available on request.
Technical data sheets can be downloaded by clicking on the adhesive name.
Adhesive | Viscosity [mPas] | Base | Curing* | Properties |
---|---|---|---|---|
Vitralit® UV 2113 | 19,000-32,000 (Rheometer, 25°C, 10s^-1) | acrylate |
UV VIS |
Acrylate hybrid superior strength low thermal expansion impact resistant low shrinkage resistant to soldering stress excellent flow properties |
Vitralit® UV 2114 | 10,000-15,000 (Brookfield LVT, 25 °C, Sp. 4/30 rpm) | acrylate |
UV VIS |
Very good adhesion to many substrates; for bonding and sealing of plastics, glass and metal |
Vitralit® UC 1618 | 500-1,000 | epoxy |
UV secondary heat cure |
high glass transition temperature high chemical resistance transparent low thermal expansion |
Vitralit® 1605 | 200-400 (LVT, 25°C, Sp. 2/30 rpm) | epoxy |
UV secondary heat cure |
low shrinkage low heat expansion very high tg excellent chemical resistance certified to ISO 10993-5 standards |
Vitralit® UC 6772 | 200-400 | epoxy | UV | Scratch-resistant, brilliant surface |
Vitralit® UD 5134 | 15,000-25,000 | acrylate |
UV VIS secondary heat cure |
Acrylate-Hybrid low thermal expansion low shrinkage impact resistant dry surface grey color |
Vitralit® 1517 | 10,000-20,000 | epoxy |
UV secondary heat cure |
low shrinkage very high Tg low heat expansion |
Vitralit® UC 6686 | 55,000-70,000 | epoxy | UV | suitable for dome coatings and "drop-effects" on glass or plastic, scratch-resistant, non-yellowing |
*UV = 320 - 390 nm VIS = 405 nm