Optically Clear Adhesives for Lens Bonding
Camera lenses, microscope lenses and lenses and prisms in optical devices such as lasers are often bonded with special adhesives, or cement, and fixed in their housing. In order not to impair the quality of the optical system, these special adhesives must not only have a high optical purity, they must also have low shrinkage in order to avoid stresses in the lens systems. The latter is often achieved by adding special fillers in the nanoscale size range.
Furthermore, prism or lens systems consisting of several lenses or prisms can also be joined together using adhesives or optical cement. These adhesives are used, for example, in cameras and optical sensors or for joining rod lenses in endoscopes. These adhesives must be highly transparent and have a specific refractive index.
As the optical components have to be fixed quickly after high-precision adjustment, very fast-curing UV adhesives are usually used here. Panacol offers special adhesives for lens bonding for both glass and plastic lenses.
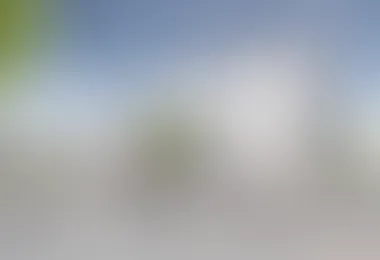
Optically clear resin adhesives are used for bonding the lenses in endoscopes
The table below lists a selection of adhesives that are suitable for lens bonding applications.
To download the technical datasheets (TDS) please click on the adhesive name. Further products and custom solutions are available on request.
Lens bonding adhesive/cement | Viscosity [mPas] | Base | Curing* | Properties |
---|---|---|---|---|
Vitralit® 1505 | 250-400 (LVT, 25 °C, Sp.3/30rpm) | epoxy | UV |
Very high glass transition temperature excellent chemical resistance low attenuation |
Vitralit® 1517 | 10,000-20,000 | epoxy |
UV secondary heat cure |
low shrinkage very high Tg low heat expansion |
Vitralit® 1527 | 600-1,250 | epoxy | UV |
Very high tg low attenuation high transmission high chemical resistance nanostructured fillers |
Vitralit® 1528 | 350-850 (LVT, 25 °C, Sp. 3/60 rpm) | epoxy |
UV secondary heat cure |
low attenuation very high Tg |
Vitralit® 1605 | 200-400 (LVT, 25°C, Sp. 2/30 rpm) | epoxy |
UV secondary heat cure |
low shrinkage low heat expansion very high tg excellent chemical resistance certified to ISO 10993-5 standards |
Vitralit® 1605 MV | 3,500-7,000 (Rheometer, 25 °C, 10s^-1) | epoxy |
UV secondary heat cure |
transparent, low shrinkage low heat expansion very high tg excellent chemical resistance certified to ISO 10993-5 standards |
Vitralit® UV 2113 | 19,000-32,000 (Rheometer, 25°C, 10s^-1) | acrylate |
UV VIS |
Acrylate hybrid superior strength low thermal expansion impact resistant low shrinkage resistant to soldering stress excellent flow properties |
Vitralit® UV 2115 | 20,000-30,000 (Rheometer, 25°C, 50s^-1) | acrylate |
UV VIS |
Acrylate hybrid superior strength low thermal expansion low shrinkage impact resistant resistant to soldering stress paste-like stable and high viscous |
Vitralit® UD 5134 | 15,000-25,000 | acrylate |
UV VIS secondary heat cure |
Acrylate-Hybrid low thermal expansion low shrinkage impact resistant dry surface grey color |
Vitralit® 6125 | 4,000-6,000 (LVT 25°C, Sp. 4/30 rpm) | acrylate |
UV secondary heat cure |
excellent adhesion to stone, glass, metals and thermoplastics medium viscosity |
Vitralit® 6127 | 20-100 (LVT 25°C, Sp. 2/60 rpm) | acrylate |
UV secondary heat cure |
high purity specially formulated for bonding glass |
Vitralit® 6128 | 800-1,200 | acrylate |
UV secondary heat cure |
very high adhesion to stone, glass, metals and thermoplastics high temperature resistance |
Vitralit® 6128 VT | 3,000-6,000 (Rheometer, 25°C, 10s^-1) | acrylate |
UV secondary heat cure |
contains chemical activator high temperature resistance high viscosity excellent adhesion to stone, glass, metals and thermoplastics |
Vitralit® 6133 | 600-1,000 (LVT 25°C, Sp. 3/30 rpm) | acrylate |
UV VIS |
High strength and impact resistance very high adhesion to glass metals and anodized aluminium transparent |
*UV = 320 - 390 nm VIS = 405 nm