UV Mask Material
UV mask material is typically used in high value component fabrication that involves processes for surface enhancement, including acid cleaning or grit blasting. Some surfaces or internal cavities may need to be insulated from these processes. Masking materials are applied to act as temporary barriers, that are subsequently removed from the completed component after processing. Applications include manufacturing of turbine components, orthopedic devices or prosthesis, or other industrial processes involving metal or nickel components.
The UV masking material is derived from light curable adhesive technology. Panacol’s family of UV light curable mask materials are solvent-free and can be easily applied and cured in seconds with a UV light source. The uncured liquid mask can be applied on components by syringe, brush, dip, or spray. All Vitralit® MASK materials provide consistent protection from high impact particulates, hot acids, alkali solutions, plating, and paint. The masks are available in many viscosities to accommodate a wide variety of component configurations and applications. Both high and low viscosity spray masks from Panacol can be easily dispensed and sprayed onto larger surfaces. Some maskants are of green color to provide better visual inspection.
Removal of Panacol mask materials with lower adhesion is accomplished by a simple peel, or a hot water dip and peel. Some maskants with very high adhesion are best removed through incineration. The materials leave no surface residue after peeling or incineration.
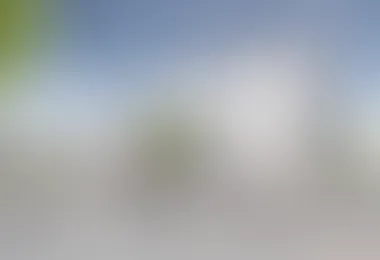
A blue colored masking product is applied in the holes of a metal part
Download:
In the following tables you will find a selection of Panacol adhesives suitable for UV masking applications. Other products or customized solutions are available on request. Technical data sheets can be downloaded by clicking on the adhesive name.
To download the technical datasheets (TDS) please click on the adhesive name.
UV masks peelable at room temperature
Adhesive | Viscosity [mPas] | Base | Properties | Removal Method |
---|---|---|---|---|
Vitralit® MASK 20104 | 14,000-17,000 | acrylate | Translucent, moderate adhesion | Peel @ room temperature |
Vitralit® MASK 20107 | 40,000-60,000 | acrylate | Moderate adhesion | Peel after hot water soak, 2-3 minutes @min. 122°F/50°C |
Vitralit® MASK 20109 | 15,000-40,000 | acrylate | Low adhesion | Peel @ room temperature |
Vitralit® MASK 20110 | 50,000-70,000 | acrylate | Very thick, low adhesion | Peel @ room temperature |
Vitralit® MASK 20111 | 30,000-50,000 | acrylate |
Mask for protective coatings, wave solder, white color |
Peel @ room temperature |
UV masks peelable in hot water
Adhesive | Viscosity [mPas] | Base | Properties | Removal Method |
---|---|---|---|---|
Vitralit® MASK 20100 | 200-400 | acrylate | Moderate adhesion, water soluble mask, dissolves in hot water | Dissolve in hot agitated water |
Vitralit® MASK E-20102-G | 8,000-15,000 (Rheometer, 25 °C, 10s^-1) | acrylate |
Green color, high adhesion, durable |
Peel after hot water soak (2-3 minutes @ mininmum 176°F/80°C) |
Vitralit® MASK 20102-G-Gel | 50,000-70,000 | acrylate |
High viscosity, green color, thixotropic gel version of Vitralit MASK 20102-G |
Peel after hot water soak (2-3 minutes @ minimum 150°F/65°C) |
Vitralit® MASK 20117 | 20,000-30,000 | acrylate |
Very high adhesion, peelable mask, green color |
Peel after hot water soak (2-3 minutes @ minimum 150°F/65°C) |
UV masks removable by incineration
Adhesive | Viscosity [mPas] | Base | Properties | Removal Method |
---|---|---|---|---|
Vitralit® MASK 20101 | 10,000-40,000 | acrylate | Hard, very high adhesion, acid resistant |
Incinerate @ 900°F or higher (approx. 500°C) |
Vitralit® MASK 20114 | 90-150 | acrylate | Low viscosity cavity fill |
Incinerate @ 900°F or higher (approx. 500°C) |
Vitralit® MASK 20115 | thixotropic | acrylate |
Controlled flow properties, extremely clean burn-off |
Incinerate @ 900°F or higher (approx. 500°C) |
Vitralit® MASK 20116 | 50,000-70,000 | acrylate | High viscosity cavity fill |
Incinerate @ 900°F or higher (approx. 500°C) |