Adhesives for (Nano-) Imprint and Wafers
Optical resins and adhesives for imprint and optical bonding applications can be used for light carpets in the automotive industry, for sensors in smart devices and wearables, or for creating structured light in projectors or time-of-flight sensing applications.
Specially formulated adhesives are available for imprint replication of refractive lenses and diffractive optical elements (DOEs). These adhesives are suitable for micro- and nano-imprint lithography (NIL), wafer level optics, and wafer bonding. These adhesives can be easily applied via puddle dispensing, spin-coating or jetting. They offer excellent adhesion to commonly used grades of glass wafers and upcoming new polymer substrates including optical grade PET or PC. Once applied and imprinted, they are quickly cured with UV light, creating a precise and durable structure on the wafer.
Highly complex optical geometries can be produced through the targeted, two-dimensional bonding of several such structured wafers with each other – and, if necessary, with so-called spacer wafers as precise spacers; this bonding technique is known as wafer bonding. Panacol has developed customized adhesives for this purpose, which are characterized by high optical quality, reliable curing in thin layers, as well as excellent mechanical properties in combination with different materials such as glass, epoxy, and metal-based masking layers.
Panacol also offers black UV-curing adhesives for black coatings and optical edge sealing. These black epoxy adhesives are permeable to UV light when uncured. After curing, they are opaque and impermeable to light.
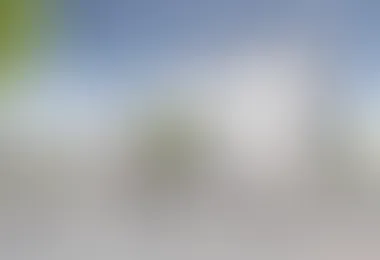
Nanostructures are printed in a very thin layer of adhesive on a glass wafer
Download:
In the following table you will find a selection of our adhesives that are suitable for various applications in the field of optoelectronics. Further products or customized solutions are available on request.
To download the technical datasheets (TDS) please click on the adhesive name.
Adhesive | Viscosity [mPas] | Base | Curing* | Properties |
---|---|---|---|---|
Vitralit® 1860 | 35.000-50.000 (Rheometer, 25 °C, 10s^-1) | Acrylate | UV/VIS |
Low coefficient of thermal expansion Low shrinkage Impact resistant Dry surface |
Vitralit® 7311 | 30-100 | acrylate |
UV VIS |
High resistance to alcohols and moisture non-yellowing very high adhesion to plastics, glass and metals suitable for bonding large areas certified according to USP Class VI |
Vitralit® BL UC 1103 | 3,500-7,000 (Rheometer, 25 °C, 10s^-1) | epoxy | UV |
black colour low shrinkage low CTE high glass transition temperature good chemical resistance resistant to sterilization |
Vitralit® UC 1632 | 80-100 (LVT, 25°C, Sp. 2/30 rpm) | Epoxy | UV |
Self-levelling High transmission Transparent, resistant to yellowing High adhesion to glass |
Vitralit® UC 1633 | 170-230 (Rheometer, 25°C) | Epoxy | UV |
High transmission Resistant to yellowing Good adhesion to glass No additional primer needed Good demolding from mold (PDMS) Halogen free |
Vitralit® UC 1658 | 75 - 200 (Brookfield LVT, 25°C, Sp. 2/30 rpm) | Epoxy | UV |
Low viscosity Flexible Low Sb-content |
Vitralit® VBB-60 | 3.500-5.000 (Rheometer, 25 °C, 10s^-1) | acrylate |
UV VIS |
Excellent peel strength Optically clear Exceptionally flexible Excellent elongation Resistant to moisture and temperature change |
Structalit® 5511 | 800-1,200 | epoxy | thermal at 60°C |
Non-conductive Outstanding adhesion to high performance plastics (LCP, PBT) High purity Electronic grade standard |
Structalit® 5531 | 5,000-10,000 (Rheometer, 25°C, 10s^-1) | epoxy | thermal at 60°C |
Non-conductive Outstanding adhesion to high performance plastics (LCP, PBT) High purity Electronic grade standard Good mechanical stability Good chemical resistance |
*UV = 320 - 390 nm VIS = 405 nm